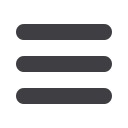

M
ay
2009
www.read-tpt.com118
›
Once at this stage of the theoretical parabolic contour, there
is a 1.39° deflection of the reflected light of the formed section’s
outset point. However, the reflected light can only be reflected to
the effective decalescence position. According to the marginal
ray principle
[4]
, all of the parallel light arrives at the effective
decalescence position after reflection by the formed section, which
shows that the spotlight performances of formed section and
parabolic contour are closed to a considerable degree.
4. Finite element analysis simulation
For practical engineering, the required parabolic parameters and
experimental model cannot be fully in accordance. The method
involves an extensive application of the feasibility of the forming
parabolic using rollforming and the accuracy of roll design.
Therefore, finite element analysis was used for the forming process
of the parabolic section in this study. Rollforming is a complicated
non-linear problem. Therefore, the forming process for the parabolic
section was simulated by the commercial FEA software MSC Marc.
4.1 Finite element analysis simulation of forming process
experiments
Because the rollforming process is very complicated, the FEA model
used in simulation should be simplified according to the practical
condition. In this study, during setup of the simulation forming
model, sheet material is deformable and the roll is rigid, and friction
force is not considered. Sheet material fed through the rolling tool is
replaced with a quarter roll sliding on the strip, and the entire long
sheet material is replaced by precut pieces of strip.
The centre distance between two stations is 250mm, and the
length of precut strip material is 300mm and the width 120mm.
The strip is divided equally to 60 elements in X-axis (transverse
direction) and 50 elements in Z axis (forming direction). There are
3,000 elements in total, and the element thickness is the practical
thickness of forming aluminium sheet (0.48mm). The element type
is No.139 with 4
nodes of thin shell.
The
simulation
geometric model is
shown in figure 9.
Boundary conditions comprise the fixed displacement at the
beginning and end of the forming strip in Z direction, and all
fixed displacement areas on the centre point of the end strip in X
direction. The Von Misses
yield and isotropic hardening criterion
were used.
In the simulation result of the forming strip, displacement in Y axis
(vertical direction) is shown as figure 10. Here different colours have
been used to represent different displacement. It can be observed
that Y displacements of the forming strip are always shown as the
same colour, which means that the length of the forming direction
of the parabolic section is uniform and the forming of the parabolic
section is comparative.
4.2 Simulation result analysis
The formed section can be compared with the simulation result. For
analysis, the experiment results had 3 corresponding sections that
keep the distance respectively of 400mm, 500mm and 600mm to
the beginning of the formed strip. For this reason, 3 sections were
picked that keep the respective distances of 100mm, 150mm and
200mm to the start of strip simulation.
Firstly, coordinates are based in the unfolding centre of the formed
section. Because of the symmetry, only the positive half axle of
transversely unfolding section coordinates is taken into account.
Then, this strip is divided equally into 6 parts, and on the divided
point, the normal error between formed section and simulation
section is shown in table 2. In the table, the positive value shows
that the simulation section is blow formed section on the divided
point, and the negative value shows that the simulation section is
formed from above on the divided point.
The mean value of normal errors of every divided point is shown in
figure 11. Given the data of table 2, the maximum error is 0.3mm. It
is observed that simulation section and formed section are basically
identical, and simulation results in high precision, so that simulating
results are reliable for engineering design.
4.3 Finite element simulation of aluminium sheet forming
process with the thickness of 0.5mm
In order to establish the thickness difference of material and roll
design setting, 0.5mm thickness aluminium sheet is used for finite
element simulation. The error is compared with a simulation strip
thickness of 0.48mm.
Sample
No.
Formed
section in Z
coordinate
(mm)
Transverse unfolding coordinate of section (mm)
X=0 X=10 X=20 X=30 X=40 X=50 X=60
1
Z=400
0 0.16 0.22 0.25 0.37 0.49 0.55
Z=500
0
0 -0.04 0.21 0.31 0.10 -0.15
Z=600
0 0.16 0.18 0.43 0.50 0.28 0.07
2
Z=400
0 -0.07 -0.19 0.04 0.2 0.14 0.11
Z=500
0 -0.06 -0.10 0.25 0.36 0.2 -0.04
Z=600
0 -0.11 -0.20 0.10 0.35 0.38 0.44
3
Z=400
0 -0.11 -0.23 0 0.13 0.01 -0.11
Z=500
0 -0.01 -0.1 0.12 0.25 0.15 0.07
Z=600
0 -0.18 -0.27 0.05 0.27 0.20 0.05
Table 2
:
A normal error between simulation section and formed section (mm)
Table 3
:
A normal error between simulation section and idea parabolic section (mm)
Formed
section in Z
coordinate
(mm)
Transverse unfolding coordinate of section (mm)
X=0 X=10 X=20 X=30 X=40 X=50 X=60
Z=100
0
-0.12 -0.2 -0.33 -0.35 -0.56 -0.95
Z=150
0
-0.17 -0.17 -0.31 -0.38 -0.5 -0.88
Z=200
0
-0.11 -0.21 -0.29 -0.36 -0.54 -0.89
Figure 9
:
Simulation
geometric model