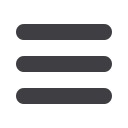

27
M
ay
2009
www.read-tpt.comT
echnology
U
pdate
›
EWI is a leading engineering and tech-
nology organization in North America
dedicated to the research and development
of materials joining and welding. The com-
pany provides materials joining assistance,
contract research, consulting services,
training, and further support to companies
across a broad range of industries.
The company has developed patented
compounds called EWI FastTIG™ which
increases the weld penetration depth of
gas tungsten arc welds (GTAW or TIG)
by as much as 300 per cent. This method
also produces consistent weld penetration
regardless of heat-to-heat variations in the
base metal composition.
In most applications, EWI FastTIG reduced
welding time by as much as 50 per cent.
For example, a typical application with
stainless steel and nickel alloys that are
welded manually in five passes require
only one or two passes using EWI FastTIG.
Welding times for these applications can
be reduced from approximately 23 minutes
for the manual procedure to 3 minutes for
a single-pass GTAW procedure using the
compound.
The mechanical properties,
weldability, corrosion resis-
tance, and safe use
of welds made with
EWI FastTIG has been
extensively tested and
proven safe for use in a
wide range of applications.
EWI FastTIG has been developed for
corresponding base materials such as SS-7
for stainless steels (eg types 304, 316, 347,
409, 410), NI-139 for nickel-based alloys
(eg alloys 600, 625, 690, 718, 800), and
CS-325 for carbon and low-alloy steels (eg
A36, SA-178C, 2 ¼ Cr-1Mo, X80).
EWI
– USA
Fax
: +1 614 688 5001
:
skhurana@ewi.orgWebsite
:
www.ewi.orgIncreasing weld penetration depth of GTAW and TIG
An EWI FastTIG compound kit
Weld macrographs, the left made without EWI FastTIG
TM
and the right
made with EWI FastTIG
Tekla and HGG have cooperated on
developing a standardized software solution
for the steel tube industry. As a result,
Tekla Structures 15 has been launched to
help produce the required control data for
NC (numerically controlled) machinery in
standard open XML format.
Tekla Structures is able to provide for all
3D tubular structures from design and
detailing to automatic fabrication. Up until
now, data transfer with tubular sections had
been possible but required several manual
operations and editing of data to complete
the process.
By completing the 3D building information
model (BIM) with a wide range of tubular
connections it is now possible to export infor-
mation to tube profiling machines by using
open XML as the new industry standard.
Tekla and HGG integrated a solution for
modelling and manufacture of tubular steel
structures. Features include a full range of
components in Tekla Structures to cover the
needs for modelling tubular structures. The
new component types are offshore saddle
(AWS) and offshore chamfer, saddle and hole,
mitre and hole, chamfer and slotted hole.
There is an integrated export of complete
manufacturing information from the model
directly to 3D tube profiling production.
The software uses an XML format-based
industry standard for transferring data
that is open to any tube profiling machine
company or design software supplier. In
addition, there is a visualization module for
3D representations of cutting shapes on
tubular structures.
All information about tubular sections can
be managed and kept up-to-date in the
structural building information model so
that all data for fabrication can be extracted
from one source. This does not require
any manual input or editing anymore.
Even complex tubular connections can be
handled automatically.
In more detail, the objective has been to
enable input of required parameters, such
as root opening, shrinkage, bevel, and pro-
file type, into Tekla Structures. The new NC
application creates the required control data
file in XML format from these parameters,
and HGG calculation module generates
contour information from this file to be used
as input when visualizing weld preparations
in the Tekla Structures 3D environment.
The NC application will be distributed as
part of the standard installation of Tekla
Structures 15 Steel Detailing configuration.
Tekla Corporation Oy
– Finland
Fax
: +358 30 661 1500
:
ig@hgg.nlWebsite
:
www.tekla.comStandardized software solution for tubular profiles
Screenshots of the new standardized Tekla Structures 15 software