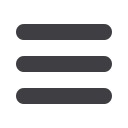

M
ay
2009
www.read-tpt.com28
T
echnology
U
pdate
›
Ultrasonic cleaning system with compact footprint
Cleaning machines for washing and rinsing components in several stages often have
their rectangular process tanks positioned end to end in a line. The Versa+ ultrasonic
cleaning machine is different, in that the Finnish manufacturer, FinnSonic, has swivelled
the tanks through 90° so that they are side by side. The installed equipment is therefore
significantly shorter, saving space on the shop floor.
Available through UK agent, Turbex, the modular, expandable machine can have
any number of tanks, which can be either 40 or 80 litres in capacity. Typical cleaning
processes include ultrasonic or immersed jet cleaning, single or multiple water rinsing
and hot air drying. Particle filtration and oil separation can be included, according to
customer requirement.
Designed for small-scale washing
and degreasing applications, the
automated process is said to result
in uniform cleaning of components.
Manual configurations can also be
specified.
The Versa+ is well suited to use in
the electronics and semiconductor
industries, PVD (physical vapour
deposition) and other coating
applications, and cleaning watch
parts, lead frames and x-ray tubes.
Each tank is operated from a panel linked to a central PLC system, which provides
ease of use and also allows retrofitting of handling automation, available for 10kg or
20kg basket weights. Manual handling by pneumatic assist lift is available for baskets
weighing up to 30kg.
Turbex Limited
– UK
Fax
: +44 1420 542264
:
john.huntingdon@turbex.co.ukWebsite
:
www.turbex.co.uk
A FinnSonic Versa
+
four-stage, automatic cleaning line
Circular saw blade
closes the gap
Swiss company SW Wil has developed a
new kind of HSS based circular saw blade,
named the PowerBlade 65. Using an HSS
vapour blade it is possible to cut up to 380
N/mm
2
with a moderate cutting speed.
With a standard HSS blade and a common
AlTiN PVD coating it is possible to cut up to
450 N/mm
2
with a reasonable lifetime and
cutting speed. TCT saw blades are normally
used above 650 N/mm
2
.
For the gap between 450 and 650 N/mm
2
there has previously been no circular saw
blade available offering an optimum solution
for cutting tubes and bars in this range. SW
Wil has introduced a complete new HSS
saw blade with a special HSS body and a
coating system featuring a higher oxidation
resistance than others on the market. The
company states that the PowerBlade 65
sets a new standard in the line between
450 and 650 N/mm
2
.
SwissCut SW Wil AG
– Switzerland
Fax
: +41 71 911 49 32
:
swwil@sw-wil.comWebsite
:
www.sw-wil.comItalian polyolefin pipe producer Wavin
has invested in complete automation
for extrusion lines, by adding two pipe
packaging machines and one picking
machine to one of its lines. The packaging
machines (Multipack model) and the
handling machine (Multipallet model) are
produced by Sica, Italy.
Complete automation of pipe extrusion lines
Wavin’s decision to invest in complete line
automation arose from the need to reduce
production costs and increase efficiency
and line productivity.
Sica Multipack machines create individual
pipe packs composed of various layers of
pipes, deposited in plastic separator cradles,
and then tied together by plastic straps.
The system was specially developed
for installation in lines producing pipes
between 50 and 160mm in diameter
and from 500 to 3,000mm in length
(plus bell end).
The company’s Multipallet machine for
pipe handling picks incoming packs,
rotates them if necessary, and places
them on trolleys in predetermined
layouts. The machine also picks
separator boards from dedicated
magazines and places them between
layers, to increase the stability of the
stack.
The system is able to process packs varying
in width between 290 and 620mm, with
a maximum height of 400mm. Maximum
productivity declared by Sica for pick up of
a single pack and its positioning on the cart
is 35 seconds for each pack.
With the introduction of the new system, the
operator can achieve complete automation
of pipe extrusion lines, with cost reduction,
increased process reliability and optimised
working conditions.
Sica SpA
– Italy
Fax
: +39 0544 81340
:
info@sica-italy.comWebsite
:
www.sica-italy.com
The new machines have enabled complete
automation of the company’s extrusion line
Wavin has installed packaging and handling machines
from Italy’s Sica