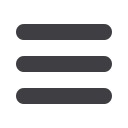

M
ay
2009
www.read-tpt.com32
T
echnology
U
pdate
›
AWS
Schäfer
Technologie
GmbH,
Germany, is the manufacturer of machines
and equipment for the mechanical forming
of pipe for power stations, shipbuilding,
and oil and gas production industry. The
company’s new series of SRMBI induction
bending machines are designed for pipe
bending of high-performance and high-
strength materials.
Induction bending involves the heating of a
pipe made from austenitic or ferritic steel by
the means of a medium frequency inductor,
to a temperature at which the yield strength
of the material to be formed is greatly
reduced, allowing the pre-determined
geometry of the pipe to be formed.
The objective of the bending process is to
produce pipe bend sections which maintain
absolute minimal wall thinning on the
exterior of the bend, as well as producing
a cross sectional form with acceptable
ovality tolerances, and producing the
desired geometrical form with respect to
radii and angular requirements. Require-
ments for bent pipes, in particular in the
energy producing industry, are becoming
increasingly stringent.
When producing steam lines, super-heaters
and manifolds, the majority of power plant
manufacturers have already initiated the
replacement of conventional materials such
as P22 with high performance materials
like P92 or Alloy 600. Due to their chemical
composition (high quality chrome/nickel/
molybdenum alloys), pipes made from
high-performance materials have a higher
long-time rupture strength, pressure resis-
tance and corrosion resistance, and can be
used under operational conditions of up to
750°C, with minimal loss of their mechanical
properties.
In pipe production, the high mechanical
properties and strength of the new materials
have a high material saving potential. As a
result, the wall thickness of a P92 pipe can
be reduced by 60 per cent compared to
pipe made from conventional materials.
The manipulation and forming of pipe made
from high-performance material with high
material strength, at the same time having
reduced wall thickness, is a new challenge
for experienced plant and machine
manufacturers. AWS Schäfer’s new SRMBI
models offer a solution with powerful
hydraulic drives, and produce bends with
high precision and quality, whether pipe
from
high-strength,
high-performance
materials or low allowed steels are being
employed.
The machines can perform three-
dimensional bends, as well as bends with
tight radii of 1.4 x D, with wall thinning of
maximum 12.5 per cent the original material
thickness at the exterior of the bend.
Bends forms of up to 182° at tight bending
R/D ratios and ovality tolerances, which
do not require re-work with additional
equipment, offer a time and cost saving in
comparison with conventional machines.
Depending on the pipe diameter, radii
to be bent, and material and thickness,
various trapezoidal forces occur throughout
the bending process that are capable of
causing changes to take place in machine
position. The can result in deviations from
the desired bending geometry.
The new machines are equipped as
standard with a newly designed braking
technique, developed in-house by AWS
Schäfer. In combination with the robust
structure with hydraulic feeding force, which
can be set with variable speed, position and
force, the SRMBI series ensures perfect
positioning precision, with the correct
feeding force at the required speed, even
when working on the heaviest of pipe work
pieces.
The machine design enables precise
bending of the most popular pipe dimensions
(diameters from 50 to 1,660mm, and wall
thicknesses from 3 to 120mm), making the
machines suitable for use in many different
industrial fields.
The bending process is controlled by special
software that allows the operator to pre-
select a geometry and to easily and quickly
program bending parameters using a touch
screen. A video screen at the control desk
allows the entire bending process to be
easily monitored at all times. This provides
additional security for the operator through
the complete bending process.
An integrated printer allows the printing of
all-important bending parameters at any
time. The use of laser optical pyrometers,
which scan a given section of the pipe
during bending, registering continual,
accurate temperature measurement of the
heat zone, ensures precise optimal bending
temperatures.
AWS Schäfer Technologie GmbH
–
Germany
Fax
: +49 2739 8700 310
:
info@aws-schaefer.deWebsite
:
www.aws-schaefer.deAutomatic bundling lines
with high productivity
Cartacci Srl, Italy, the supplier of complete
cold drawing and straightening machine
lines, has produced two new automatic
bundling and finishing lines for tubes.
One of the two new automatic bundling
lines was designed for tubes with diameter
of 125mm for a customer in Germany, and
the other for tubes with diameter of 272mm
for a Russian customer located in Voljskiy.
Cartacci offers equipment that provides
high productivity through reduced operator
intervention and an entirely computer-
based working system. The new bundling
lines were designed to have reduced
maintenance costs, and were customised
to the specific requirements of each
manufacturer.
Cartacci Srl
– Italy
Fax
: +39 035 290514
:
info@cartacci.comWebsite
:
www.cartacci.comAdvanced generation of induction bending machines
for heavy pipes
AWS Schäfer’s SRMBI can accurately bend even
the heaviest of pipes
Induction bending involves heating the pipe by a
medium frequency inductor