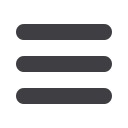

P
roduction &
P
rocessing of
A
utomotive
T
ube
M
ay
2009
www.read-tpt.com58
›
George A Mitchell Company is the
manufacturer of variable wall tube drawing
systems that can accommodate drawing
of tubular shapes, such as square,
rectangular and hexagonal cross sections.
These are used for products such as
automobile crush tips and frame tubes,
as well as truck and SUV axle tubes, all
of which are produced in North America
for the automotive market by Mitchell’s
customers.
Mitchell and its customers have long
standing relationships that extend over the
past 25 years, where
many special forming
processes have been
jointly developed to
enhance the tubular
products fabricated
for the automotive
industry,
sporting
goods and tubular
parts industries.
Mitchell is a leader in
providing production
equipment to produce
variable wall
tubes used in making cylinder
blank tube for power steering assemblies,
SUV and truck axles, as well as instrument
panel beams and automobile fuel tank
filler tubes.
Mitchell is also the world leader in producing
hydraulic tube push pointers in capacities
ranging from 5,000lb up to 1,000,000lb, for
materials from aluminium to zirconium, for
the tube drawing industry.
With over 600 push pointers produced and
delivered worldwide in the past 48 years,
no other company on the globe can match
Mitchell’s push pointing expertise and
machine design.
George A Mitchell Company
– USA
Fax
: +1 330 758 7263
:
sales@mitchellmachinery.comWebsite
:
www.mitchellmachinery.comVariable wall tube drawing line for truck and SUV tubes
A Mitchell variable wall
tube drawing line
Corrosion of heat exchangers for automotive
air conditioning units can be a major
problem. The unit is often located near the
front grille of the vehicle and is exposed to a
severely corrosive environment. Road salts,
rain and high temperatures all contribute to
high corrosion rates. Arcsprayed zinc offers
resistance to corrosion, lower production
costs and reduced pollution, compared to
other processes.
Multi-void aluminium tubing is used in the
production of serpentine type condensers,
which are widely used in air conditioning
systems. The voids in the tubing provide a
route for the cooling medium to extract heat
from the incoming air. The coating of the
tubing and the corrugated fins is generally
carried out by flux brazing or zincate
nocolok brazing processes. In either case,
problems are inevitable.
Whether the air is extracted from the top
or the bottom of the air conditioning unit,
cleanliness is critical to the process, as
is production reliability. The advantages
of zinc sprayed tubing include improved
productivity and zinc deposited at a pre-
selected rate. In addition, a zinc diffusion
pattern equally uniform to the zincate
process is produced.
Spraying with zinc also means highly
corrosive flux, zincate treatment and waste
treatment are not required and post brazing
cleaning processes can be eliminated.
The zinc coating is carried out in line
with the extrusion press. The plant can
be installed on to either new or existing
lines. The number of individual arcspray
pistols required depends on the number of
extrusions being produced by the press.
The pistols are located on adjustable
mounts, angled to allow even coverage
and can accommodate single of multi
strand extrusions. Metallisation has over
145 units in use around the world, with
some companies opting for 1.2mm wire
to produce a very fine coating finish for
specialist surface protection.
The Metallisation Arc 528E is a heavy
duty, high performance arcspray pistol,
which features a unique constant geometry
head. This proven head ensures reliable
alignment of the wire for long periods,
giving consistent spray quality and ease of
maintenance. The electric drive, electronic
control system and constant geometry
spray head combine to give a wide range of
deposition rates to match the job size.
The Arc 528E supplies pack and wire feed
includes power cables, air hose and control
cable. For multi-void mills, a quick release
option is also available, as this dramatically
reduces the complexity of the system and
pistol changeover time.
The S250 Energiser is a reliable, consistent,
low current power supply, which has been
specifically designed for arc spraying.
With a PLC control it offers reliability and
ease of maintenance. For added reliability,
its control electronics panel is sealed to
reduce dust ingression, has easy access
energiser panels and an external fuse bank
for reduced mean time to repair.
Metallisation Ltd
– UK
Fax
: +44 1384 237196
:
sales@metallisation.comWebsite
:
www.metallisation.comUnique solution for multi-void tube spraying
The Arc 528E is a heavy duty, high performance
arcspray pistol
A diagram of the system layout