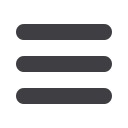

P
roduction &
P
rocessing of
A
utomotive
T
ube
M
ay
2009
www.read-tpt.com62
›
Plants–dies for sheets and tubes
UNIT OF HYDRAULIC DRILLING
COMPACT MODULARS OF LIMITED SPACE
MECHANIC CLOSING END EXTRACTION
NO MAINTENANCE
CONSTRUCTION OF
SPECIAL UNITS OF
HYDRAULIC DRILLING, TRANSFER
MACHINERIES FOR TUBES AND COMPONENT
OF THE AUTOMOBILES INDUSTRY
SPECIALIZED
IN UNIT OF SCALLOP CUTTING,
SHEARING, DRILLING WITH UNITS OF
RADIAL PASS AND LINEAR
MENEGON ENNIO S.A.S.
Via G. Barbarigo, 30 – 36060 ROMANO D’EZZELINO (VI)
ITALIA
Tel./Fax +39 0424/570880 e-mail:
menegonennio@gmail.comTogether with the automotive supplier
Faurecia, Jansen has developed special
precision steel tubes for the rear seat
construction of the Audi Q7 SUV. The
successfully completed project is a
good example of co-engineering: the
mutual development of a product by two
specialised technology partners.
Jansen Ltd, Switzerland, supplies a wide
range of international customers with high
quality precision steel tubes. By beginning
close collaboration at the earliest stage, it is
possible to define the materials and product
specifications together with the client. This
saves development costs and time, and
the time to market-readiness is significantly
decreased.
The rear seats of the Audi Q7 were
developed by Faurecia, one of the most
significant automotive supply companies in
the world. The rear seat concept in the Q7
offers multiple configuration possibilities.
The rear seats can be folded down and
stored away as needed so that a flat loading
surface up to the front seats is created.
For the sub-construction of the rear seats,
cold-rolled precision steel tubes from
Jansen were delivered in five different
sizes. Depending on the type of seat,
round, rectangular or flat-oval tubes are
used.
The definitive forms and models of the steel
tubes were developed by Jansen, together
with Faurecia. Various grades of steel, wall
thicknesses, strengths and elongations
were made and tested in the course of
prototyping.
Jansen Ltd
– Switzerland
Fax
: +41 71 761 22 70
Website
:
www.jansen.comComfortable car seats with precision tubes
Jansen Ltd is a specialist for welded precision
tubes
Round, rectangular and flat-oval tubes for rear
seats in Audi Q7
A comprehensive service
for automotive tube
components
Kolsatpol sp zoo, Poland, is a specialist
in production of metal elements for the
automotive industry in the field of metal
machining (tube and bar). Products
manufactured by Kolsatpol are assembled
in automotive brands such as Fiat, Opel,
Toyota, and Volvo.
The company’s range of final products is
4mm to 81mm diameter, with a length from
10mm to 350mm. Kolsatpol carries out
operations including cutting, chamfering,
drilling/reaming, boring, threading and
shaping.
Kolsatpol’s aim is the permanent assurance
of product quality, proven with certification
from quality systems ISO 1400:2004 and
ISO/TS 16949:2002.
Kolsatpol sp zoo
– Poland
Fax
: +48 33 816 93 95
:
dariusz.kuznik@kolsatpol.comWebsite
:
www.kolsatpol.comTube mills specifically developed for automotive products
Officine MTM SpA, Italy, is the manufacturer
of tube mills for the automotive industry.
The company began manufacture of these
mills in 1984, with the first application
being a complete tube mill for tubes in high
tensile carbon steel, with small OD and
thick material.
Since that time several tube mills have
been developed specifically for automotive
products, for carbon steel, stainless
steel and aluminium alloys in different
applications.
MTM currently has a comprehensive range
that can satisfy most requirements of tubes
for automotive industry. For carbon steel
tubes, the company offers its expertise
with complete tube mills for seats, shafts,
engine supports and frames. Exhausts are
made in aluminized and galvanized carbon
steel as well as in HF welded stainless
steel.
For aluminium radiator and heat
exchangers, MTM has a specific range of
complete solutions for welded and folded
tubes, as well as charging air cooler
sections. The company also has experience
in manufacturing tube mills for hydroforming
applications.
Due to its partnership with Atomat,
a worldwide leader in design and
manufacturing of roll sets for the tube
industry, MTM can offer turnkey plants
complying with the highest quality standard.
Officine MTM SpA
– Italy
Fax
: +39 041 999611
:
sales@mtmtubemills.comWebsite
:
www.mtmtubemills.com