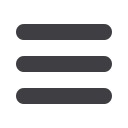

P
roduction &
P
rocessing of
A
utomotive
T
ube
M
ay
2009
www.read-tpt.com66
›
www.linsinger.comInclined Bed Circular Saws
Dr. Linsinger-Str. 24
A 4662 Steyrermühl,
Tel. +43 7613 88 40,
Fax +43 7613 88 40-951
maschinenbau@linsinger.comFor seamless tube, for-
ging and rolling mills
2 Euro per Cut
Cutting time: approx. 2:30 min.
(Ck45, Ø 380 mm)
Hall 7
Booth A24
Visit us!
Rotary swaging is a cold forming process.
Compared to other forming processes rotary
swaging stands out due to its advantages
in the processing of tubes. The advantages
of the process gain increasing importance
due to the current developments in the
environment and waste disposal policy.
This method can improve the economy
compared to other competing manu-
facturing processes. Thus more and more
applications come to the focus of the
development. Rotary swaging features all
advantages of cold forming, such as short
process times, exacting tolerances, plane
surfaces and material savings due to the
avoidance of chips.
All metallic materials that can be formed
are suitable for rotary swaging. In case of
steel this ranges from mild steels to alloy
steels up to stainless steel. There is also
no problem in using non-ferrous materials
such as aluminium, magnesium, titanium
and their alloys.
In addition to material savings, the
process also offers considerable potential
in weight optimisation. The savings are
highest in case of changeover from solid
material to tube. In order to follow this
path economically, a process is needed
that can form the requested geometries at
the internal and external diameter of the
workpiece ready-to-fit or at least near-net-
shape.
Rotary swaging offers forming possibilities
that would be difficult to achieve using other
forming processes. The forming possibilities
at the internal and external diameter enable
a weight-optimisation at the workpiece.
The method can be used to manufacture
cylindrical and conical bores with excellent
Weight optimisation of workpieces in the automotive industry
Tubular drive shaft
Hollow transmission shaft
Piston rod for shock absorber for passenger cars
Headrest rod out of stainless steel