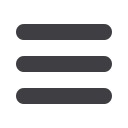

P
roduction &
P
rocessing of
A
utomotive
T
ube
M
ay
2009
www.read-tpt.com56
›
RSA, a German sawing technology
specialist, has launched the Rasacut XS,
a high-performance circular saw for tube
diameters from 6 to 25mm. The machine
was developed as a response to recent
technological developments in the field
of circular saws that have generally been
aimed at high output of the 10-100mm
diameter range.
The minimisation of variants in the
automotive industry is leading to larger
batches for the production of semi-finished
products made from tube, hollow sections
and solid bars. However, quality demands
are also increasing. A machine concept
aimed at a wide spectrum of workpieces
can cope only to some extent with
demands made by highly specific parts,
eg line systems in the automotive sector,
where extremely strict requirements are
applied concerning the degree of purity and
precision of the tubes. However, the large
quantities allow comparatively low piece
costs.
Multi-cut or bundle cut saws are generally
used for the production of large batches in
the diameter range up to 25mm. However,
aimed at an improvement in quality and
lowering of piece costs, the new RSA
development counts on the single cut. The
fully automatic processing cycle – even for
large fixed lengths of 2,000mm or longer –
presents an essential advantage.
When working with bundle
cut saws, tubes are
manually bundled. The
workpieces are counted,
fixed with an adhesive
tape and inserted into a
prismatic guide that feeds
the tube bundle to the
saw. With the Rasacut XS,
tubes are automatically
singled and fed. This
method also allows one
person to operate several
saws.
The new RSA system is beneficial
during further processing of tubes
after cutting. In case of bundle cut
saws, fixed lengths can fall apart after
cutting – the so-called ‘mikado effect’.
The feeding of the tubular sections
to another processing step, such as
deburring, requires further logistics –
either an automatic singling machine
or the manual feeding of a magazine.
The Rasacut XS can be modularly
expanded into a processing centre,
combining in one line the processes of
sawing, deburring or facing and chamfering,
checking of lengths, roundness or chamfer,
cleaning and stacking.
In the experience of the RSA developers
and designers, another argument for the
single cut concerns the quality of the parts.
Apparent motions in the tube bundle or in
the layer can lead to scratches on the tube
surface. Due to minimal misalignments
within the tube bundle, parts are outside of
determined tolerance.
RSA claims that the Rasacut XS achieves
in a single cut output values that are as
high as those of multi-cut or bundle cut
saws – and depending on the dimensional
range, even more – due to the reduction of
ancillary times. Material is fed by means of
a gripper with an acceleration of up to 40
m/s². The next tube is fed during the current
sawing process, avoiding a loss of time
during the changeover to the next stock
length.
On the basis of the Rasacut XS output
values, around 150 changeovers to the
next stock length are required per hour
for a tube with 8mm diameter and a fixed
length of 250mm, for a stock length of the
random material of 6,000mm. This example
shows the importance of ancillary times with
regard to the total output. As an example of
output: round tube with a diameter of 12mm
and a wall thickness of 1mm, material
Latest saw specifically designed
for small diameters
The newly developed Rasacut XS for tube
diameters from 6 to 25mm
The central clamping of workpieces facilitates the use of saw blades with
small diameters and high speed
Two gripper feeds reduce to zero the ancillary times for a
changeover to the next stock length
The Rasacut XS
automatically singles the
tubes from the crane
bundle and feeds them
to the saw