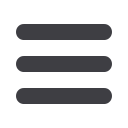

2016 CORPORATE SOCIAL RESPONSIBILITY REPORT (CSR)
4
HUMAN RESOURCES INFORMATION: HR DEVELOPMENT AS A DRIVER OF PERFORMANCE
In the United Kingdom, in the same way as in France, special attention
is paid to workstation ergonomics. For example, within four weeks of
being hired and after each move to a new workstation, employees are
asked to fill in a questionnaire assessing the extent to which their work
environment, equipment and resources are aligned with the needs of
their job. The completed questionnaires are reviewed and any identified
problems or weaknesses are corrected. UK employees are also actively
encouraged to take an eye test every two years, paid for by the
Company.
In Germany, eye tests are also offered to all employees and occupational
health physicians are on hand to examine employees exposed to
specific risks.
4.3.4.1.2 GUARANTEEING WORKPLACE SAFETY
The Group’s workplace accident frequency rate is very low compared
with the industry average in France, at 2.21% in 2016 compared with
2.51% in 2015. The severity rate also improved year-on-year, standing
at 0.05%
versus
0.08%.
These results were achieved thanks to the many preventive initiatives
deployed by the Group. For example, over 800 hours’ safety training
was given to AEOS line managers and supervisors through half-day chat
sessions designed to alert them to day-to-day risks. In 2017, preventive
measures will be stepped up in the energy and major construction
project (ITER, EPR, etc.) sectors, through the development of a safety
culture focused on the sharing of experiences between employees and
clients.
Over the years the Energy & Infrastructure division’s business has tended
to include more engineering projects comprising general contracting
and prime contracting support, particularly in the nuclear sector.
This change in the business, together with the ever-more stringent
requirements of clients and the French Nuclear Safety Authority, has
led to the adoption of a more assertive nuclear risk management policy.
In 2014, the division published a charter describing its nuclear safety
culture in France. The charter reaffirms the division’s awareness of
its responsibilities towards employees, clients and the Nuclear Safety
Authority. It presents the nuclear risk management policy and extends
the continuous improvement process in the areas of quality, safety and
environmental protection.
The charter lists the principles that Assystem and its partners and
subcontractors pledge to uphold:
●
stringent application of the laws, regulations and standards applicable
to clients, supported by internal control measures adapted to each
situation;
●
continuous improvement of the safety processes and culture, with a
sustained focus on training and knowledge-sharing;
●
integration of labour, organisational and human factors in the nuclear
risk management process;
●
exchanges based on trust and vigilance to ensure transparency.
These principles are translated into commitments that are monitored
using indicators and are the subject of an annual joint assessment by
the teams and clients in the relevant sector.
Rather than nuclear risks, road accidents are the main source of accidents
within the Group, during employees’ daily commute or business travel.
To reduce the incidence of road accidents in France, Group management
decided to completely rethink its awareness-raising and prevention
policy to meet the goal of zero accidents resulting in bodily injury where
an employee is at fault.
Several initiatives were launched in 2016:
●
during European Mobility Week in September 2016, an awareness-
raising campaign was organised among employees in France on
eco-driving techniques and road safety (reminder of road safety rules,
opportunities to try out a driving and crash simulator, etc.);
●
leaflets were sent to the members of the French workforce with
a driving license, raising their awareness of the very real risk of
accidents during their daily commute or on their way to or from
client sites;
●
the vehicle utilisation charter was revised and enhanced with the
addition of preventive messages and warnings about the consequences
in terms of liability of failing to respect the Highway Code.
In 2017, eco-driving and road safety training will be organised for
employees in France who have a driving license. In addition, as from
2017, in the event of an accident where a Group employee is at
fault, the employee concerned will be invited to meet with his or her
unit’s health and safety correspondent to discuss the circumstances of
the accident.
Employees who have the use of a company vehicle are now required
to sign a vehicle utilisation charter covering such topics as accident
prevention and liability in the event of a breach of the Highway Code.
In addition to encouraging more responsible driving, two other means
of protecting employees from the risk of death or injury on the road
have been identified:
●
ensuring that vehicles are properly maintained and that drivers pay
attention to the information and warnings displayed on on-board
computers;
●
promoting alternatives to individual car travel, to reduce driving time
and the related risks; examples include videoconferencing, ride-
sharing, use of public transport, car-with-driver solutions for trips to
and from stations and airports, carpooling (see Section 4.4.2.1 of
this Registration Document).
In the United Kingdom, the Health and Safety General Policy Statement
defines strict workplace safety standards.
ASSYSTEM
REGISTRATION DOCUMENT
2016
56