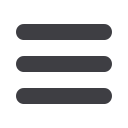

Finishing and end f inishing
www.read-tpt.com86
J
uly
2014
Belt grinding of heavy bars and
tubes from India
GRIND Master offers a trolley-type
machine for belt grinding and finishing
of large diameter and heavy bars and
tubes. The machine has heavy-duty
roller supports to take up the tube/bar to
be ground. It also provides the rotational
drive to the job being ground.
The floating belt grinding heads
operating from the top are specially
designed to take care of bend and
ovality in tubes. These heads are
mounted on a long trolley, which is rigid
in construction. The machine has very
easy settings to ensure quick change
over from one job size to another.
Tubes/bars from 60mm to 300mm
diameter can be ground.
Grind Master
– India
Email:
sales@grindmaster.co.inWebsite:
www.grindmaster.co.inTwin cutting and workpiece
finishing from Rattunde
RATTUNDE
Corporation,
a
manufacturer of finished length tube
and solid bar production, has introduced
the ACS
®
+ CFMtwin machine, the
latest in the company’s range of tube
production systems. Equipped with
a specially designed twin machining
head that fits onto the standard head,
the new machine can cut two tube or
bar sections simultaneously, and then
machine both ends of both workpieces,
also simultaneously.
The new machine can produce up to
5,000 finished pieces per hour, and the
option also exists for single tube or bar
production on the same machine.
The ACS + CFMtwin machine,
when in twin mode, can process two
workpieces of 10 to 41.5mm OD
each into finished lengths from 10 to
1,500mm. As an example: 21mm OD
x 3.5mm wall x 45mm length cut from
a 6.5m mill length of stock material,
based on carbon steel. When the
twin head is removed, the standard
machining head can process a single
workpiece up to 105mm OD.
In addition to the twin workpiece
processing, the new Rattunde machine
offers the OEM or production house all
the capabilities found on Rattunde’s
ACS family of tube and bar production
systems, including secondary brush de-
burring, end machining (chamfering and
facing), inspection, washing, drying and
robotic packaging. The entire machine
and all auxiliary workstations are
motion-controlled by CNC from a single
operator station for maximum efficiency.
The ACS + CFMtwin is built on the same
platform as the existing Rattunde ACS
+ CFM and ACS + CFMcurve systems.
Other standard features on the new
machine include data management on
all workpiece parameters (approximately
10,000 workpieces), data logging
of every part produced for full part
traceability, material lead and end edge
detection for minimised crop cut and tag
end. All operating limits are set from the
control panel, with continuous tool break
monitoring for the saw blade and all
cutting tools.
Even when processing in twin mode,
the set-up time for a new job can be
under 15 minutes, according to Rattunde
engineering.
Because
the
machine
offers
essentially double the production in
the same machine footprint, up to 40
per cent energy savings have been
documented on a 25mm OD x 3mm wall
x 42mm long piece from a stock length
of 6m in a typical batch count of 45,000.
Rattunde Corp
– USA
Fax: +1 616 940 2771
Email:
company@rattunde-corp.comWebsite:
www.rattunde-corp.comClose-up of twin cutting head: the machine
cuts two workpieces simultaneously
Each end of the two workpieces is simultaneously
chamfered before automated transfer to the
cleaning and final packaging stations