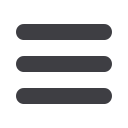

Finishing and end f inishing
www.read-tpt.comJ
uly
2014
87
Tube end forming
equipment
MANCHESTER Tool & Die supplies tube end forming, grooving
and crimping machines and tooling to a variety of industries, with
machines ranging from
3
/
16
" to 3" OD capacities. Standard and
custom-built machines and parts can be manufactured to meet
customer applications.
The company’s manufacturing facility is available for customers’
production machining needs such as CNC and manual turning,
CNC and manual boring, CNC milling, grinding and wire EDM.
Steel fabricating services are also available.
Manchester Tool & Die recently introduced a servo positioning
flag stop system, designed to aid set-up personnel in quickly
adjusting tube out through the machine’s HMI (human machine
interface). The system provides consistent adjustments resulting
in quicker set-up times. The servo positioning system is available
for newer M71 and M82 machines that are equipped with HMIs.
Manchester Tool & Die, Inc
– USA
Email:
brblocher@mtdbkb.comWebsite:
www.manchestertoolanddie.comSurface improvement technologies
for bars and pipes
LOESER GmbH is a major producer
of grinding, polishing and deburring
machinery and a global leader in
technology required to produce super
high quality surface finishes.
From very simple one-station
machines to completely automated
multiple station systems, Loeser
custom engineers the system to each
customer’s exact requirements.
Headquartered in Speyer, Germany,
Loeser has been in operation since
1934 producing machines and complete
systems for over 75 years. Loeser
has persistently continued to further
develop and refine existing fundamental
technologies.
Loeser pressure controlled grinding
technology allows for heavy stock
removal, tolerance grinding and fine
finishing. Quick abrasive belt changing
offers amajor time advantage compared
to stone grinding or turning. Loeser
machines can be equipped with multiple
stations in different combinations,
completely enclosed or open style.
Systems are fully modular and easy
to upgrade with additional stations to
grow with future requirements.
Loeser prides itself in innovation
using the latest technology in machine
controls and mechanical components.
This keeps Loeser on the cutting edge
of developing process advancements,
and allows it to offer much more than
just the construction of a machine.
Loeser actually invents customers’
solutions.
Working closely with major abrasive
belt manufacturers and their latest
technology keeps Loeser ahead of the
competition.
Loeser offers technologies for
centreless stainless tube mirror
polishing/buffing. In addition to standard
belt grinding and polishing machines for
round and flat parts, Loeser provides
creative solutions for micro finishing up
to 0.004µm Ra.
Loeser prides itself in innovation
using the latest technology in
machine controls and mechanical
components. Loeser’s product line
has been expanded with new solutions
for extremely high stock removal,
continuous through feed induction
hardening and continuous through feed
chrome plating.
Pressure controlled grinding and
polishing combined with new Loeser
innovations make it the only producer
of surface finish technology systems
capable of offering all of the following
solutions: through feed induction
hardening; through feed belt grinding
and finest polishing before plating;
through feed continuous chrome
plating; through feed polishing post
chrome; and through feed wax buffing
for added corrosion resistance.
Careful and accurate evaluation of
each customer’s specific requirements
is Loeser’s highest priority. The
accumulated knowledge from many
years of process development and
innovative thinking is key.
This is absolutely critical in order to
construct large, complex automated
systems. A complete Loeser system
can be installed and running at a
customer’s plant in a remarkably short
amount of time. Loeser’s customers
benefit from decades of experience
in developing thousands of grinding
processes.
Loeser GmbH
– Germany
Fax: +49 6232 31 4850
Email:
info@loeser.comWebsite:
www.loeser.com