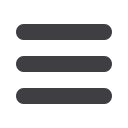

CAPITAL EQUIPMENT NEWS
AUGUST 2016
36
A
s much as 80% of an engine rebuild
comprises parts and the balance engi-
neering and testing, providing fleet oper-
ators ample opportunity to save costs. However,
selecting the correct diesel engine replacement
parts requires a thorough understanding of the
important role that they play in the long term
viability of any equipment operation.
Enterprising fleet operators are saving costs
on their diesel engine parts by striking a del-
icate balance between quality and price, but
these decisions have been guided by expert
opinion that place plant availability right at the
top of the agenda.
“Astute fleet operators demand that they at
least receive the operating hours that were
guaranteed by the parts supplier and the pro-
vider of the engine rebuilding or repair service.
They understand that risks involved in making
poor decisions can have major adverse im-
pacts on their businesses further down the
line,” says Andrew Yorke, operations director
of Metric Automotive Engineering.
Metric Automotive Engineering is the exclu-
sive African distributor of IPD parts. The cur-
rent IPD product line offers wide and deep
coverage for engines in the older CAT 300
series to the later CAT C series, allowing Met-
ric Automotive Engineering to supply critical
componentry at a very competitive price.
Adverse cost cutting principles
Fleet operators have come under significant
pressure due to low commodity prices and a
slowdown in infrastructure spending, and cost
cutting practices have become inevitable to
ensure survival. However, Yorke tells
Capital
Equipment News
that he is concerned that
some procurement departments are making
short term decisions that are having a
significant impact on the sustainability of
their businesses.
Important decisions are being made without
the necessary technical input from personnel
at the operational and workshop levels.
This has sometimes led to original parts being
procured without exploring the performance
of cost effective alternatives that exceed the
original equipment manufacturers’ (OEM)
specification.
In extenuating circumstances, procurement
departments opt for cheap parts without con-
sidering the mandates of operational depart-
ments that have to keep essential items of
equipment operating efficiently.
These parts are sourced from Asian countries
at vastly reduced prices, but carry no warranty
and the quality of their workmanship can be
questionable.
“Unfortunately, costs are being cut in the
critical areas of the operation. The reality is
that these businesses have been built upon
the efficient operation of their equipment and
their viability is being compromised by these
practices,” Yorke says.
He says the risk associated with buying cost
effective alternative parts can be easily mitigat-
ed by consulting the expertise of diesel engine
specialists. Metric Automotive Engineering was
appointed IPD’s distributor based on its long
track record providing a quality engine rebuild-
ing service to prominent fleet operators in the
mining, construction and industrial sectors.
Metric Automotive Engineering’s customers
also respect IPD’s leading standing in the in-
ternational diesel engine sector. The company
has been manufacturing high quality diesel
and natural gas engine components since
1955, and the workmanship of its compo-
nents is backed by its ISO 9001:2000 certifi-
cations and comprehensive warranties.
However, it is the extensive work done by IPD
to improve the performance of critical compo-
nents that has enabled it to retain its compet-
itive edge in global load-and-haul industries.
A sound example of this is its patented one-
piece friction-welded piston that includes an
oil gallery as part of the original casting. This
removes inherent design weaknesses in two-
piece pistons with their steel crowns and alu-
minium skirting.
A proactive response
“IPD’s research and development efforts
are a proactive response to modern high
performance engines with their higher
combustion pressures and temperatures.
Our customers expect their parts suppliers
to be well ahead of the innovation curve in
line with the sophisticated machinery they
deploy on their sites,” Yorke says.
Importantly, the R&D agendas of leading en-
gine OEMs are creating higher barriers of entry
for component manufacturers and, in many
instances, exposing the limitations of many af-
termarket pistons, bearings and liners.
Yorke says this has already exposed the
inadequate performances of pirate parts
which have significantly underperformed
in these arduous environments, resulting in
very steep learning curves for unsuspecting
fleet operators.
Conventional materials used to make liners,
for example, are no longer sufficient for the
high horsepower of these engines. Liners have
to be hardened to increase their resistance to
wear and have been designed to be stable,
eliminating movement inside the engine.
IPD responded to this demand many years
ago when it introduced high tensile seamless
steel tube cylinder liners with a wedge design
that continue to outperform their traditional
cast counterparts, and Yorke expects them to
become standard replacement parts.
The ‘yellow’ equipment industries are facing
what is probably one of their most challenging
periods. Lowering total operating costs and
boosting productivity are essential to survival.
Metric Automotive Engineering and its prin-
cipal have a solution that strikes that critical
balance between cost and quality.
b
IPD PARTS REV FLEET OPERATORS’ PERFORMANCES
IPD Parts are manufactured in an ISO 9001:2000
certified facility and R&D ensures the latest
materials and technology are leveraged for optimum
performance.
Andrew Yorke, operations director of Metric
Automotive Engineering.