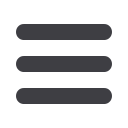

20
CONSTRUCTION WORLD
APRIL
2015
PROJECT PROFILE
Logistics
The only way to travel to St Helena is by sea, and a round trip between
Cape Town Harbour, or Walvis Bay and St Helena (weather permitting)
is roughly 20 - 22 days. This makes logistics a key issue for BRSHAP.
Basil Read, the main contractor, set up bonded forwarding facilities
in Walvis Bay and Cape Town to consolidate materials and plant from
all around the world. A temporary jetty in Rupert’s Bay was built to a
depth of five metres with six mooring points to accommodate a modi-
fied ship that was sourced from Thailand – the NP Glory 4.
The ‘roll on roll off’ ship, was modified to carry 1 million litres of
fuel below decks and was fitted with a 13 m high crane that can move
30 ton container loads of material anywhere on deck. With a carrying
capacity of 2 400 tonnes, it has already completed 32 voyages from
Walvis Bay to St Helena and transported over 50 000 tonnes of cargo,
including 10 million litres (pumped ashore via a floating line), explo-
sives, cement, fly ash, admixtures, sand, construction equipment, rein-
forcing steel and other materials needed for the project. The NP Glory
4 is the first ship to ever touch land and offload directly onto St Helena.
Planning is vital due to the long logistical chain and is carried out well
in advance.
Scope demands a variety of skills
The project required a diverse range of expertise in the different disci-
plines of project management, design, blasting, logistics, road and civil
construction, open cast mining, steelwork, crushing, concrete tech-
nology and commercial building.
The project design had to be practical, giving careful consid-
eration to St Helena’s unique geology, logistical challenges,
limited specialists on the island, materials supply and was adapted to
maximise flexibility of resources.
Dry Gut
St Helena’s lack of flat land was a challenge. The airport is being built
on Prosperous Bay Plain which is made up of ravines that the locals
call ‘guts’. In order to create a runway, these guts had to be filled. The
ENDING
ISOLATION
The Basil Read St Helena Airport Project
(BRSHAP) is a design, build, operate and hand
back contract for an international airport in
St Helena. Situated in the South Atlantic Ocean,
St Helena is one of the most remote islands in
the world – 2 000 km from the nearest mainland.
It has with limited infrastructure, no major
construction equipment, few construction
materials, not even sufficient sand and no
harbour – presenting a unique challenge
for Basil Read.
biggest gut – Dry Gut – spans over 400 m on the southern end of the
runway and was filled with over 8-million m³ of blasted andesite and
basaltic igneous rock and soil to the depth of over 100 m. This quan-
tity would fill 20 Mbombela Stadiums to the roof. A total of 503 day
shifts, 439 night shifts, six days a week, with 450 000 truckloads were
used to fill Dry Gut.
In order to achieve compaction, 1,2 million litres of water was
pumped daily from 16 boreholes into four storage dams. The boreholes
were drilled to avoid interference with St Helena’s water supply.
To minimise settlement with the variable quality of the material,
materials management and rockfill processing had to be conducted
with stringent controls. A settlement monitoring system was
installed into Dry Gut fill at several levels to monitor the fill during and
after construction.
A 260 m long and 120 m wide and 30 m deep open channel was
excavated in the adjacent valley to deviate any rainfall water runoff.
Initially, the design called for a 2 m diameter culvert to run through the
fill but the channel required less maintenance and provided additional
620 000 m
3
of quality fill material.
Haul road
A 14 km haul road with up to 15° gradients was constructed along the
side of a mountain between Rupert’s Bay and the airport site. The road
is used to transport heavy equipment and construction materials from
to the airport site. At the end of the contract, the road will be developed
into a public road. This road winds, twists and rises over 500 metres in
the first three kilometres, an engineering and construction challenge
on its own
Airport runway
Cost effectiveness, the mountainous terrain of the island and
the environment were key elements influencing the design of
the airport runway. Concrete was chosen over asphalt in order to mini-
mise future ongoing maintenance.
Manufactured from 27 000 m³ of concrete using a Wirtgen Paver,
the runway is mostly unreinforced, measures 1 950 m long, 45 m wide
ST HELENA’S