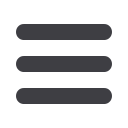

21
CONSTRUCTION WORLD
APRIL
2015
PROJECT PROFILE – STEEL CONSTRUCTION
with a maximum thickness of 350 mm and reduced thickness to the
‘off-keel’ sections.
Basil Read took a number of measures to prevent the freshly paved
runway from plastic shrinkage and cracking. Vinyl tarps were used to
cover the pavements during initial curing – protecting the concrete
from St Helena’s sun and rain. In addition, CHRYSO Fibre Plus (micro
fibres) were added to the concrete mix design and CHRYSO Cure WP
(white pigmented curing compound) was applied to pavements.
Terminal building and combined building
Significant care was taken with the design of the buildings as they
will be the first introduction to St Helena. They have been designed to
blend in with their surroundings with a focus on functionality. They are
energy efficient, with a sloped roof, clad in locally mined stone with
concrete canopies and a glass façade. A brick making machine was
installed on site to manufacture an estimated 250 000 bricks.
It was decided to use underground cabling to reduce the visual
impact of power lines and achieve an obstacle limitation surface for
the airport. The cabling follows the alignment of the runway, further
reducing the construction footprint and avoiding environmentally
sensitive areas.
Bulk Fuel Installation (BFI)
Basil Read are also responsible for the design, construction and
commissioning of a 6 million litre BFI and an Airport Fuel facility.
Permanent wharf
The design and construction of a permanent wharf for ships up to
100 m long will be of great benefit to the island, as ships will be able to
dock for the first time in the island’s history.
Historical data on the wind and swell conditions of Rupert’s Bay
were used to carry out modelling tests at Stellenbosch University.
Environmental studies and surveys of the sea bed and surrounds were
taken to assess any environmental impact of the work.
The wharf comprises a rock breakwater using 1 600 concrete 7 t
Core-loc
©
armour units and 400 concrete 27 t main block units, which
are being manufactured in a precast yard in Rupert’s Valley. Two
200 tonne crawler cranes will place these precast units in position
via GPS. The placing is tricky due to their weight and the sea
conditions and currents.
As the units are exposed to sea water, the concrete had to be
durable, and quality control is extremely tight. To obtain a quality
product, the concrete had to have good workability. A CHRYSO plasti-
ciser, Omega 101, also used on the runway, assisted in creating a good
surface finish.
Risk management
Risk Management is absolutely crucial to the project. Risk registers
have been created with over 200 identified and rated risks and specific
mitigation measures allocated to each risk. These registers are vital in
identifying, mitigating and avoiding risk and maintaining the project
Project information
• Project start date:
December 2011
• Project end date:
February 2026 (Phases I and II)
• Main contractor:
Basil Read
• Client:
St Helena Government and Department for Inter-
national Development
• Project value:
R4,6-billion
MAIN:
The NP Glory 4 is the first ship to ever touch land and offload directly
onto St Helena.
TOP:
The BFI tanks fully painted.
ABOVE:
The biggest gut – Dry Gut – spans over 400 m on the southern end
of the runway and was filled with over 8-million m³ of blasted andesite and
basaltic igneous rock and soil to the depth of over 100 m.