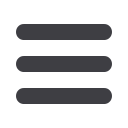

24
CONSTRUCTION WORLD
APRIL
2015
Since the ABI plant had been built
using a very specific ‘origami style’
roof, a contractor with both this
specific proficiency and an exten-
sive track record in the commercial and
industrial maintenance sector was required.
PROJECTS AND CONTRACTS
STATE-OF-THE-ART
ROOF
When the time came for Amalgamated Beverage Industries
(ABI) to refurbish the roof of its bottling plant in Devland,
it looked for a business that has earned a reputation in the
industry for its expertise in dealing with unusual roof designs.
FROM TOP TO BOTTOM:
The origami steel roof, showing signs of serious
corrosion.
Opal White polycarbonate sheeting, with
sisalation visible underneath.
Zinc alum 0,55 mm roof sheeting.
>
Based on previous experiences with the
organisation, ABI turned to R&D Contracting
to solve its roofing challenges.
The ABI bottling plant in Devland is a
world-class manufacturing site, which has
been producing cool drinks for the South
African market for decades. However, as
with any older facility, the plant’s roof was
reaching the end of its natural lifespan,
having become victim to corrosion, caused
by the harsh vagaries of South African
weather. The engineers who originally built
it adopted an ‘origami style’ for the roof,
which utilises very specifically folded steel
that is designed to be self-supporting.
When it came time to replace the roof,
says David Williams, managing member and
technical sales director at R&D Contracting,
retaining the origami style was not cost-ef-
fective. Although self-supporting, it utilises
large volumes of steel. “We decided to base
the design of the new roof on a previous
project we had completed for ABI at its
Wadeville Coca Cola canning plant,” he says.
Williams explains that the project
currently sees R&D removing around six
tons of steel from the roof every week.
This is being replaced by a far lighter zinc
aluminium composite – known as zinc alum
– that is just 0,55 mm thick. He states that on
average, the company is installing between
12 and 18 metres of the new roofing per day.
The galvanised support beams are
specially designed for the project, and are
certified by engineers, prior to implementa-
tion, he adds. Williams also points out that
R&D is using sisalation underneath the zinc
alum roofing for the purposes of insulation.
This is also far thinner than the previous
insulation used, but thanks to a reflective
coating on the outside, is just as effective at
keeping the factory cool.
“The sisalation is a key innovation here,
as it improves vastly on the old roof, which
utilised sponge, fitted between double
steel, for insulation purposes. Sponge works
fine in a new roof, but as the roof ages, it
becomes easier for this sponge to get wet.
I can tell you that vast tracts of wet sponge
add an enormous additional weight load
onto the roof. Fortunately, this is all negated
now by the far lighter zinc alum roofing and
the sisaltion we are using instead.”
Intense preparation
Williams explains that the project is expected
to take approximately 10 months from site
set-up to conclusion. This, he adds, does
not include the additional time required for
preparation and fabrication prior to starting.