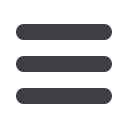

Mechanical Technology — March 2015
5
⎪
On the cover
⎪
Above:
Assembly of a 750 rubber-lined mill circuit pump
at the Weir heavy bay foundry.
Left:
Weir Minerals offers a range of equipment solutions
including hydrocylones, rubber lining, hoses and slurry
valves.
mining efficiencies
hydrocyclones and Isogate
®
valves.
“The market has definitely changed.
What is vital is the duration of any shut-
downs and improving intervals between
these shutdowns. Equally critical are the
health and safety considerations around
handling and repairing equipment.”
Weir Minerals Africa has ISO 9001,
ISO 14001 and OHSAS 18001 ac-
creditation, and considers these factors
in product development decisions and
holistically in terms of repeatability and
reliability.
“Another major consideration is the
environmental impact of the products we
produce. A good example is being able to
reclaim scrap metal from our customers
and to reprocess that at our Heavy Bay
Foundry (HBF) in Port Elizabeth and
at our Isando foundry facility to limit
the impact on raw materials usage and
improve costs. The quality of our raw ma-
terial stock is a major factor in ensuring
our products meet stringent quality and
performance standards,” Fawcett says.
“We have sophisticated design pack-
ages that allow us to optimise both
performance and materials of construc-
tion, which means employing the right
material where it is required. In addi-
tion, we investigate the root causes of
wear occurring in specific areas and use
this data for product and future product
enhancements,” Fawcett says.
Such enhancements flow through
to the existing Warman AH
®
range in
order to increase efficiency and wear
performance. “The new Warman WRT
®
impeller and throatbush upgrade kit has
been used to make significant improve-
ment to the design of the component
combination,” Fawcett explains. These
are integral components of the pump
that impact on its hydraulic and wear
performance.
The Warman WBH
®
slurry pump of-
fers more than a dozen enhancements
to the already state-of-the-art Warman
slurry pump range. Here the main fo-
cus is on meeting the productivity and
cost demands of Weir Minerals Africa’s
customers in different operating environ-
ments. “This pump is destined to set a
new benchmark in slurry pumping stan-
dards, as the Warman AH range is widely
accepted as the benchmark for many
applications over the last few decades,”
Fawcett says.
The Warman SLR
®
pump is designed
specifically for medium-duty slurry han-
dling where conditions are not arduous
enough to justify a heavy-duty slurry
pump. “We revisited the way our pumps
are put together from a maintenance
perspective. Traditionally, components
were split radially, which was the easi-
est way to strip a pump down and then
reassemble it. Our particular innova-
tion in this regard is to split the pump
axially and fit it with a one-piece volute
that reduces the assembly and risk of
any potential component mismatch.
The overall outcome is a pump unit
with a significantly smaller footprint
to what is currently in the market.”
Looking at general sump applications,
Fawcett says the Warman WBV
®
ultra
heavy-duty range of vertical cantilevered
slurry pumps has been launched and he
believes that this too will be set to rede-
fine these applications. The new design
features internal agitation as opposed to
a mechanical agitator attached to the
impeller. The impeller has specialised
vanes that take up a certain amount of
the flow and divert it back into the sump
to produce the agitation required. This
feature is proving far more successful
than the traditional mechanical or water
assisted agitation mechanisms.
Several of these next generation
sump pumps are being trialed. “We have
completed the test periods and have
removed the pump units to evaluate
the wear performance. The result has
exceeded our expectations and it will
be a game changer for our customers,”
Fawcett says.
“This development is emblematic of
our approach to develop products for
specific applications, rolling them out
across our entire product offering and
then standardising at a higher level. This
means that all design changes are incor-
porated into subsequent improvements
and then finally in the standard product
offerings. This, in turn, means that these
improvements are passed on to all of our
customers. Thus, as replacement compo-
nents are purchased, the full benefits are
realised,” Fawcett concludes.
q