
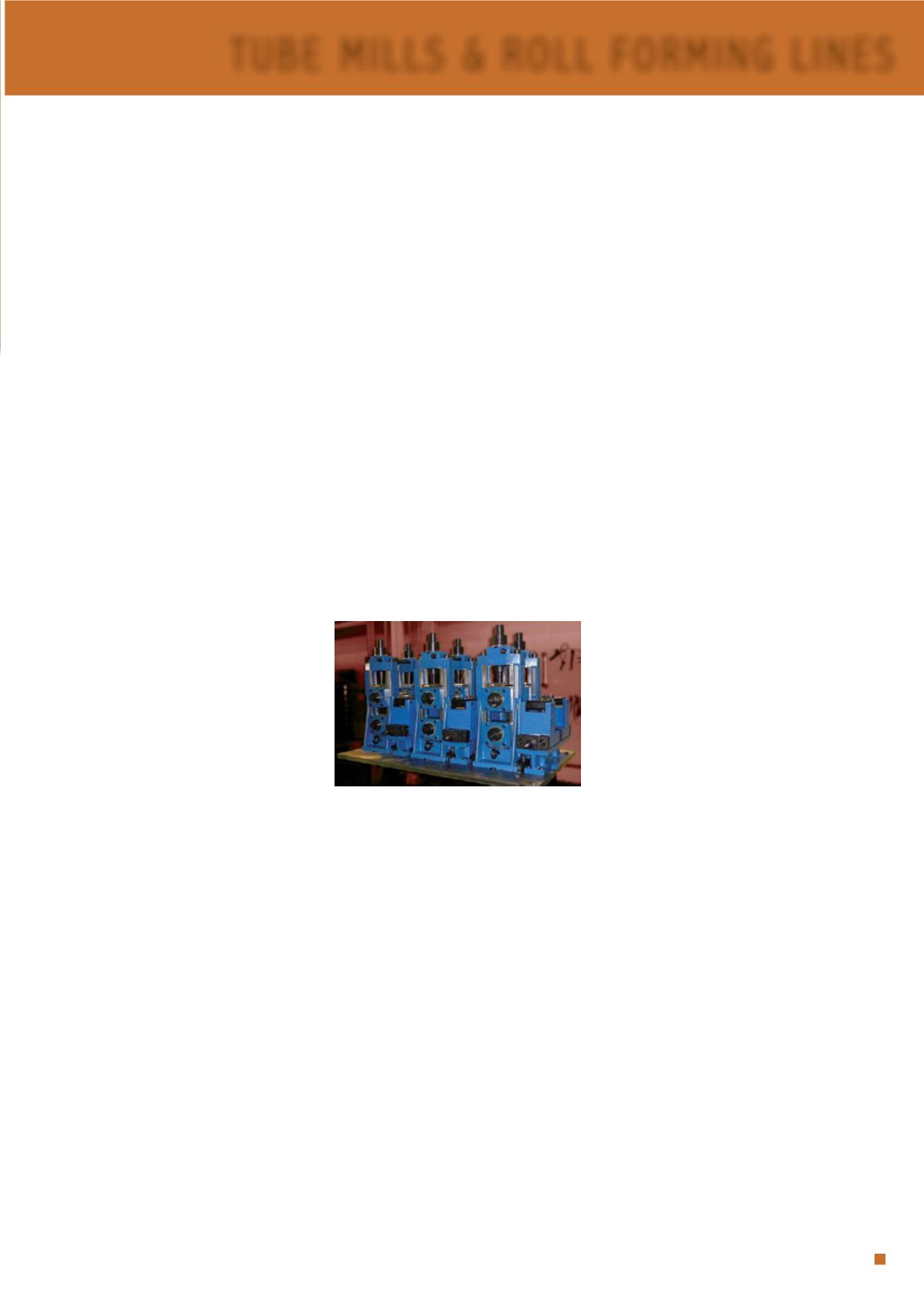
J
ULY
2016
65
T UBE M I L L S & R OL L FORM I NG L I NE S
Rafter upgrades McKay tube mill
RAFTER Equipment Corporation has
shipped a new RT-3000 tube mill re-top
and drive train upgrade for a major North
American automotive tube producer. The
equipment will replace older McKay tube
mill equipment that is worn, difficult to
maintain and has outlived its useful life.
The McKay machine had integral roll
stands and gearboxes making it difficult
tomaintain and to upgrade the drive train.
By switching to conventional universal-
shaft driven roll stands, the drive train
can be tailored to the customer’s needs.
In this case, the addition of a four-speed
transmission allows for both high torque
on the more difficult products and high
speed on the easier products. The
customer’s existing mill drive system
and motors will be utilised.
Rafter worked with the customer to
ensure compatibility with their existing
mill base and HFI welding equipment.
The new driven and idle side roll stands
are mounted on sub-plates that will be
permanently secured to the existing mill
bases without the need to change the
passline height of any of the ancillary
equipment. These roll stands include
mainy updated features to reduce and
simplify maintenance. In addition, the
roll stands will be more robust than the
ones they replace.
Rafter Equipment Corporation is a
manufacturer of tube mills, pipe mills,
roll forming machines, cutoff machines
and other related tube and pipe mill
machinery. Additional services include
rebuilding and upgrading mill equipment.
Originally started in 1917, the Rafter
name is known for reliable, high-quality
tube mill and roll forming equipment.
Rafter Equipment Corporation
– USA
Email:
sales@rafterequipment.comWebsite:
www.rafterequipment.comUniversal Tube to rebuild
Abbey Etna 3X tube mill
UNIVERSALTube &RollformEquipment
Corp, a worldwide supplier of used
tube, pipe and rollform machinery, was
commissioned by a returning customer
in the first quarter of 2016 to rebuild an
Abbey Etna 3X tube mill.
Universal Tube custom built a new
weld section for the tube mill. The
custom-built base was topped with
a new two-roll weld box and an EPU
(seam guide).
Universal Tube built the base, and
installed the weld box, EPU and a new
double scarfing unit with automatic
quick-lift tool holders to complete the
weld base components. The weld
base was then installed in-line with the
tube mill.
Universal Tube & Rollform imple-
mented a complete re-work of the
Abbey Etna 3X tube mill to match the
customer’s existing line. The re-work
included new spindles as required, all
new bearings and seals, re-worked
side closers, and new AC motors and
AC vector control system provided by
Universal Controls Group.
For over a quarter of a century
Universal Tube & Rollform has supplied
used tube, pipe and rollform machinery.
This latest order is an example
of how the company has expanded
its capabilities to better serve the
requirements of a growing and diverse
customer base. Its partnership with
controls supplier Universal Controls
Group has enabled it to offer a wide
array of services.
Universal Controls Group offers
expandable mill control systems that
are pre-engineered or custom built to
customer specifications.
Universal Tube & Rollform
Equipment Corp
– USA
Fax: +1 419 874 2825
Email:
sales@utubeonline.comWebsite:
www.utubeonline.comRafter has shipped a new RT-3000 mill
Roll machining technologies and solutions
ROLL Machining Technologies and
Solutions has been offering tube mill
operator training for many years. It
continues to listen to its customers’
needs and to evolve training to make it
relevant to every individual plant.
In the first half of 2016 there has been
a dramatic increase in the amount of
new and refresher training that has been
requested. Rick Olson, RMTS president,
stated: “The onsite operator training
we provide is second to none. The
operators are learning from people who
have been in their shoes. We take the
operator approach and teach from our
hands-on experience in these situations.
That is the best way one can teach the
troubleshooting skills the operator needs
to perform at their best.”
RMTS will develop a training class
for any specific product and teach the
operators safe working habits that will
increase efficiency and productivity.
Each operator that completes the training
is awarded a certificate of completion as
an RMTS certified tube mill operator.
RMTS also offers several classes on its
exclusive series of DVDs so companies
can offer operators new training and
refresh training at their own pace.
Roll Machining Technologies
– USA
Website:
www.rollsolutions.com