
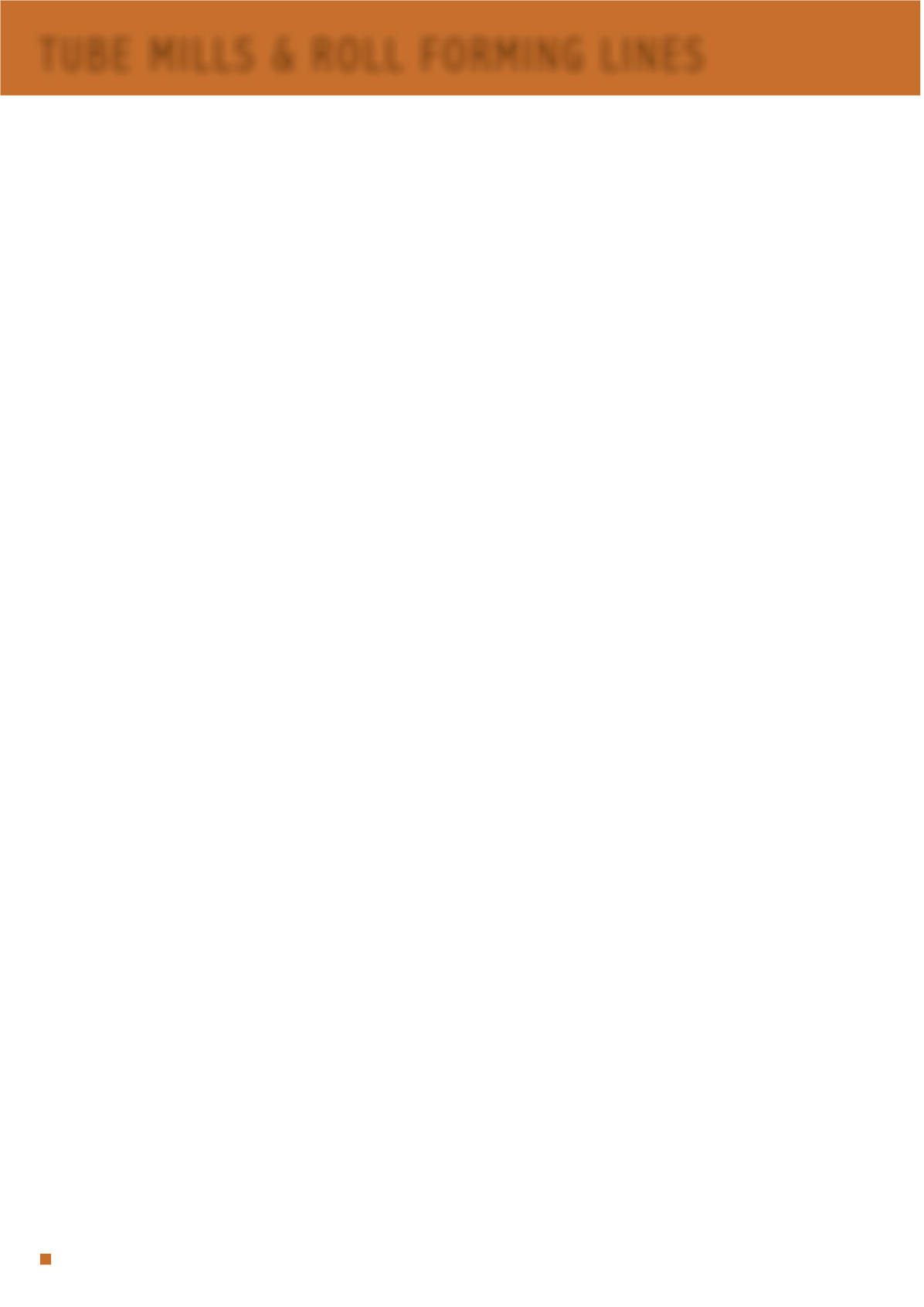
68
J
ULY
2016
T UBE M I L L S & R OL L FORM I NG L I NE S
Pipes and couplings manufacturing line
DANOBAT has opened a new pipes
and couplings manufacturing line for the
company Tubos Reunidos.
The new facility is equipped with
Danobat machines for the manufacture
of threaded pipes and hoses. The project
is the result of a joint venture between
Tubos Reunidos and Marubeni. The
premises total around 31,500m
2
, and
include a workshop where the Danobat
machines manufacture the threaded
pipes.
The new production line will
manufacture
highly
technological
pipes, specifically threaded for drilling
and production of oil and gas wells.
Danobat machines finish off the pipes
with patented premium threads that are
claimed to provide superior performance.
“They are perfectly suited for work on
sites at 4,000 or 5,000 metres depth,”
explained Carlos San Martín, director of
technology and development of Tubos
Reunidos Industrial.
Among other facilities, the line will
have several horizontal Danobat TTB
lathes for the machining of pipes. One
of the most important features of this
machine is the rigidity, high production
and chip removal capacities during
turning and threading operations. In
addition, it is provided with load-unload
systems, positioning channels and
solutions with specific tools for turning
pipes.
The line will be equipped with Danobat
band saws to cut the pipes, offering
a high value-added comprehensive
solution to Tubos Reunidos.
In the new factory, Danobat machinery
will also produce the necessary special
couplings to join the pipes in the well.
Danobat
– Spain
Website:
www.danobatgroup.comNakata 30" ODF Mill line
NAKATA Mfg Co, Japan, is preparing
to deliver its first orbital die forming mill
for large welded pipes to a Chinese
pipe manufacturer following the recent
installation of a small pipe mill of the
same type equipped with a laser welder
at a Japanese customer.
The pipe size is up to OD 30"
(762mm) and WT 25.4mm, and most
of the products are API line pipes up to
X80 grade. The metal strip used in roll-
forming is typically coiled with a width
of less than 2m. This means the roll-
forming process is only applied to the
production of pipes below 26" OD and
beyond that press forming processes
such as UO and JCO have to be used.
Theoretically, it is possible to produce
pipes larger than 26" OD using the roll-
forming process if plates can be used as
raw material instead of coil. In practice,
however, it is difficult for roll-forming to
process the plate stably because of its
limited length.
In addition, irregularly deformed
pipes, at both the nose and tail ends, are
caused by strong contact between the
plate and rolls during threading, resulting
in very low material yield compared to
the continuous process, which is a big
obstacle to the application of roll-forming
in the plate-by-plate process.
However, in this 30" ODF mill, these
problems can be solved by adopting
ODF technology to both the breakdown
and finpass section, resulting in a very
stable and productive hybrid forming
process.
This innovative technology also has
other advantages in the production of
ultra-thin wall pipes and pipes made
of hard-to-work material, as well as
excellent performance in high-speed
laser welding.
Nakata Ltd
– Japan
Email:
sales@nakata-mfg.co.jpWebsite:
www.nakata-mfg.co.jpStainless steel tube making technology
KUSAKABE Electric and Machinery Co is
celebrating its 100
th
anniversary this year.
Its first complete stainless steel tube mill
installed in China was in Suzhou City, in
2010. This is a high frequency induction
welding stainless steel tube mill.
Many HF SUS tube mills have been
supplied around the world over the
past 20 years. The product range of the
Suzhou City tube mill is Ø32 to 65mm,
thickness 0.8 to 2.5mm, maximum line
speed 60m/min, and cutting length 4,000
to 6,000mm. The largest consumer of
HF welded SUS tubing is the automotive
exhaust industry.
The major advantages of this tube mill
are production yield and output. The yield
of prime products has been more than 97
per cent since production commenced
and the customer is delighted with this
result and the continuing level of technical
support, according to Kusakabe.
Kusakabe equipment is built for
durability, repeatability and reliability.
Output from the Suzhou City tube
mill is 1,500 to 1,800 tons per month.
Kusakabe designed and manufactured
the tube mill using its experience to take
full advantage of automation tomaximise
operator and machine productivity while
producing a consistent, high quality
product with minimum variation of all
the inputs. The tube mill contains many
of Kusakabe’s technologies, such as
strip forming for SUS, weld temperature
monitoring and control, internal weld
bead height adjustment while running,
quick change tooling for rapid OD
changes, data logging system of all
the variable inputs for engineering and
quality checking, tracking and auto
rejection of all defect tubing.
A new tube mill is to be delivered and
installed in the USA. The size range of
this tube mill is Ø45 to Ø54mm, thickness
1 to 1.5mm, line speed 15m/min and cut
length 700 to 2,200mm. After cutting, the
products do not need to be re-cut and
they go straight to the next process.
Kusakabe Electric and Machinery Co,
Ltd
– Japan
Email:
sales@kusakabe.comWebsite:
www.kusakabe.com