
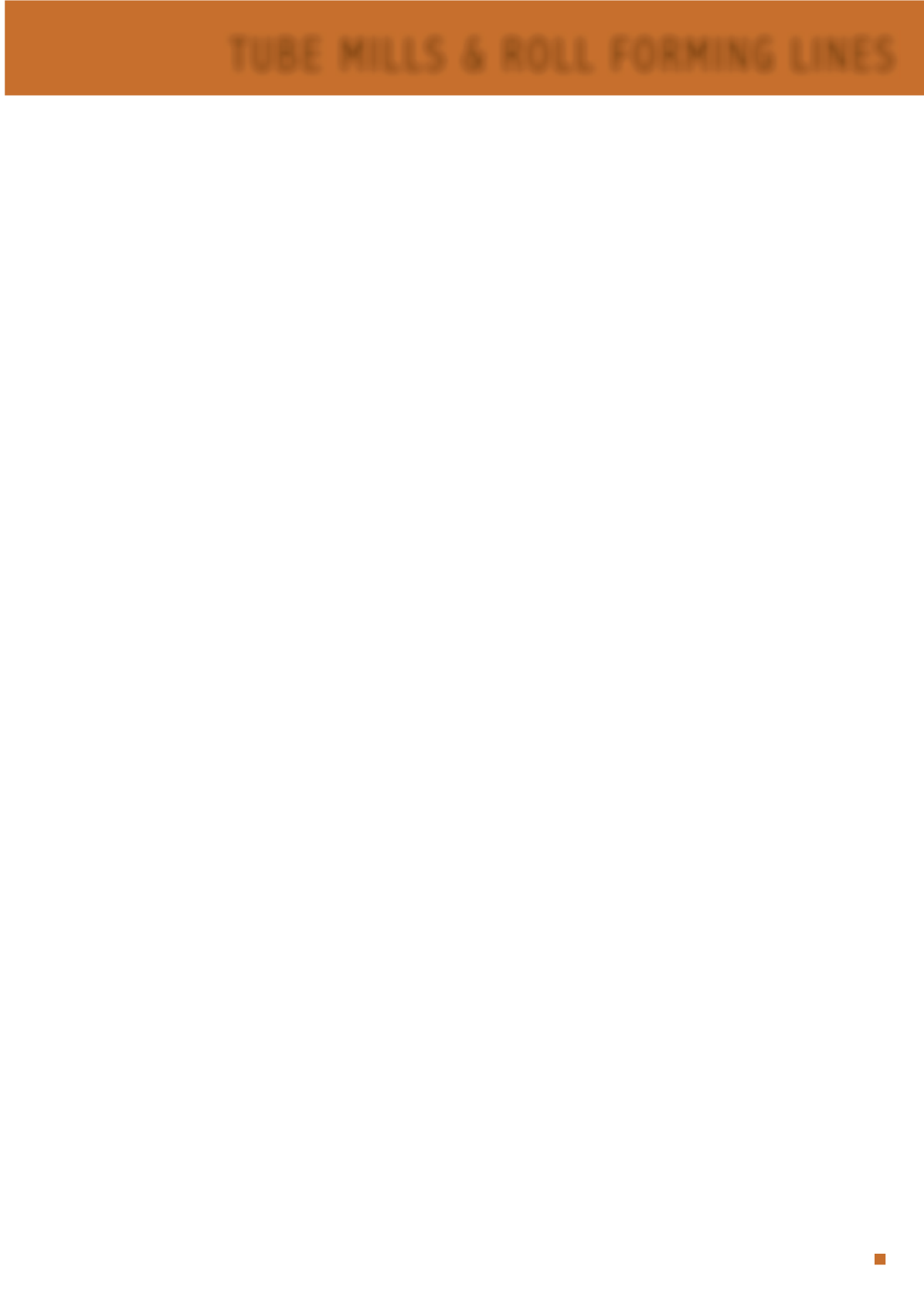
J
ULY
2016
69
T UBE M I L L S & R OL L FORM I NG L I NE S
Dual-capacity, high frequency tube mill
T&H LEMONT has delivered a new
dual-capacity quick-change tube mill
system, developed to handle increasing
demands for JIT deliveries of welded
tubular products. The dual-capacity
mill will allow for a greater range of
production diameters in a minimum
amount of floor space.
In effect, the dual-capacity mill gives
the tubing producer the ability to produce
a range of tubing normally produced on
two mills. It also represents a smaller
initial investment to produce a larger
range of tubing diameters.
The entire entry and exit equipment
remains unchanged, as does the basic
mill base and drive system.
The dual capacity of the mill is
achieved by two sets of quick-change
subplates designed to mount on a
single base system and utilise one
drive system.
In this instance, one set of subplates
with 3.5" shafts was designed for
producing tubing from 1.25" to 5",
and a second set of subplates with 6"
shafts was designed to produce tubing
from 2.5" to 8" diameter. The distance
between the stands is optimised for the
diameter of tubing produced on each
set of subplates.
As with all quick-change systems, one
set of subplates is in production while
the second set of subplates is available
for change-over.
The mill, which produces standard
mechanical rounds as well as hollow
structural shapes, is designed to
utilise the customer’s overhead crane
to change over the subplates. The
subplates are held to the base by a
hydraulic clamping system, allowing
them to be connected and disconnected
from the base quickly and efficiently.
T&H
Lemont
has
provided
technologies to produce products such
as stainless steel hypodermic needles,
communication cables, flexible tubular
products, high-strength welded and
roll-formed shapes and large diameter
API pipe.
In addition to complete production
systems, the company provides a
variety of components and services
to the tube, pipe and roll-forming
industries. Services include tube and
pipe roll design and manufacturing, mill
alignment and operational consulting.
Components offered by T&H
Lemont include welders, cut-offs,
entry equipment, accumulators, pre-
punch, post-punch, seam orientation
stands, weld boxes, edge conditioners,
bead scarfing systems, straightening
systems, single point adjustment
systems, dedimplers, blades, jaws and
roll shafts.
T&H Lemont Inc
– USA
Fax: +1 708 482 1802
Email:
sales@thlemont.comWebsite:
www.thlemont.comQuick-change tech for mills and roll forming
RAFTER Equipment Corporation has
introduced a new patented Mill-Flip
®
quick-change technology for tube mill and
roll forming machines that promises part-
to-part changeovers in 15 minutes or less.
The new system requires no
special mill stands or roll tooling, no
complicated mill drive connections or
electrical controls systems, no special
operator or maintenance training, and
no overhead cranes or special raft
handling equipment. It features the
ability to quickly break into a production
run and quickly go back to the previous
product, as well as built-in redundancy
for increased line up-time, and no
infringement on the operator’s side of
the mill during changeovers.
The company also manufactures tube
mills, pipe mills, roll forming machines,
flying cut-offs and other related mill
machinery. Its business includes the
retrofit and replacement of common
tube mill components, including driven
roll stands, idle side roll stands, weld
squeeze boxes, weld upset bead
removal equipment (OD bead trimmers)
and turkshead type straighteners.
Rafter Equipment Corp
– USA
Fax: +1 440 572 3703
Email:
sales@rafterequipment.comWebsite:
www.rafterequipment.comComplete line for precision steel tubes
TUBE mill equipment supplier ASMAG
has shipped a complete line to
manufacture up to 4" high-precision steel
tubes to a customer in the USA. The
comprehensive line comprises a fully
automated 600kN triple draw bench with
integrated pointing machine, and a fully
automated finishing line consisting of a
ten-roll straightener RRM-pro-100/10,
testing table, multiple sawing line,
chamfering units and a stacking, bundling
and banding system.
The requirements of the line were to
achieve savings on production costs
and a simultaneous increase in quality
of the products made. Modern drive
technology and innovative machinery
concepts in addition to a high degree of
automation allow for faster production
speed and higher availability of the line.
The placement of all equipment in-line
and the resulting elimination of manual
material handling between the individual
components of the line resulted in
significant reduction of scrap.
The customer benefits from ASMAG’s
quality and consistent manufacturing
standards, a single point of contact, and
seamless integration of all machinery,
equipmentandcomponentsintoareliable,
comprehensive line. Together with
Seuthe, the ASMAG group of companies
focuses on design, manufacture, supply
and service of solutions and equipment
for the manufacture of high quality steel,
stainless steel and non-ferrous metal
tube, pipe, profile, bar and wire products.
ASMAG GmbH
– Austria
Fax: +43 7616 880144
Email:
sales@asmag.atWebsite:
www.asmag.at