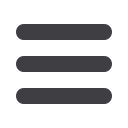

40
CONSTRUCTION WORLD
FEBRUARY
2016
One of the trends within the
construction sector relative
to cranage and heavy lifting
is the resurgence of the use
of heavy precast elements
in construction projects.
This, according to Quentin
van Breda, technical
director of Torre Lifting
Solutions and founder of SA
French, will require much
larger tower cranes than
those typically used on a
construction site.
Commenting on the role of tower
cranes on construction sites, Van
Breda says that their use in terms of
material being handled has varied
over the years. “Originally tower cranes were
seen as general materials handling tools.
They handled almost everything that needed
to be lifted and moved, and this included
large skips with concrete. In the past, slabs
were most commonly poured using tower
cranes,” he says.
Fast track projects
This, however, changed as more and more
projects became fast track. “Fast track project
schedules meant that concrete needed
to be placed faster and where the bulk of
concrete being used was for slabs, pumping
became more common place,” Van Breda
says. “This meant that tower cranes were
handling general materials and when it came
to concrete placement the cranes were used
only for the pouring of columns.”
Van Breda says that with this move
towards precast solutions, Torre Lifting
Solutions has seen an increasing number
of enquiries for tower cranes capable of
handling heavy precast elements such as
flooring slabs on new construction projects.
He says it is significant because this type
of lifting requirement doubles the lifting
capacity of the tower crane required.
“In the normal construction environment
everything is equated to cubic metres of
concrete, and the equation for lifting would
then be, say 2,5 t to be lifted at the required
maximum radius of 50, 60 or 70 metres,” Van
Breda explains. “The entire scenario changes
in the case of heavy precast elements as these
could be as heavy as 4 t to 6 t but would still
need to be lifted at the same radii.”
Good for using cranes
This move towards precast elements is a good
one for industry as the utilisation of much
larger cranes will inevitably result in quicker
cycle times on site even when moving other
materials. Van Breda says that this will make
for greater productivity with the subsequent
cost savings in labour and time.
“What is however noticeable is that few
contractors in South Africa own this size tower
crane, with the population in this category
probably no more than10 in the country,” van
Breda says. He says that a standard run-of-
the-mill tower crane used at the top end on
a construction site for traditional materials
handling would be a 200 mt machine, but in
the case of handling heavy precast elements
the bottom end tower crane would need to
be 385 mt.
The Potain MCT 385 is a topless crane
which is easily erected with a mobile crane,
and the load chart is ideal for lifting heavy
precast panels at increased radii, while
providing the construction site with the addi-
tional flexibility and convenience that a tower
brings to a project.
Even though this is a big tower crane, the
individual components never exceed
10 t and this, according to van Breda, ensures
that erection and disassembly fall within the
parameters of normal mobile cranes.
“This is particularly important where
space constraints exist and this is, as all
contractors know, always a factor with urban
construction projects.”
It was designed jointly by Manitowoc
engineers in Europe and Asia to serve several
types of markets, and offers a 2 metre mast
with a maximum free standing height of
64,9 metres. This compact mast, along with a
compact jib design and a streamlined counter
jib, make the tower crane easy to assemble
and transport. “This is a major advantage on
crowded urban projects,” Van Breda says.
Telescoping the crane is made easier
as the hook height can be 50 metres above
the last anchor points, and in addition, the
design allows for internal climbing on high-
rise applications.
With a 20 t maximum capacity, the Potain
MCT 385 is equipped with frequency-con-
trolled mechanisms for hoisting, trolleying
and slewing, facilitating smooth movement
and precise positioning. This is an important
feature when handling and placing such large
precast elements. Van Breda says
that servicing the mechanisms is straightfor-
ward as they are conveniently located and
easily accessible.
“The larger Potain towers will be
supported through the same infrastructure
as all Potain tower cranes, and this includes
technical input and support from the time
of specifying the crane through to erection
by skilled technical teams. Ongoing mainte-
HEAVY PRECAST
elements resurges
>