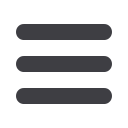

S
eptember
2008
www.read-tpt.com44
T
echnology
U
pdate
›
Application of innovative technologies –
TWP
®
(tailor welded plates)
Gräbener Maschinentechnik GmbH & Co KG, Germany, has successfully
commissioned a second TWP
®
plant (TWP = tailor welded plates). The company is
an established manufacturer of machines for SAW pipes, such as plate edge milling
machines, bending presses, 3 roll bending machines, and post-bending presses.
This system consists of a two-side plate edge-milling machine with integrated laser
hybrid welding unit. After two-sided edge preparation, plates with different plate sizes
and plates of different materials
are positioned together in one
clamping (welding gap 0) to be
welded by means of subsequent
laser hybrid technology.
The idea to join plates with
different materials and plate
thicknesses into components has
been known for a long time and
has been achieved recently in
the industry. Good examples of
application are in the automotive
and shipbuilding industry.
In the area of shipbuilding, the benefits gained from using this machinery includes
higher productivity, fewer required straightening operations, and higher component
accuracy.
The laser hybrid welding and the tailor-welded-plates principle are innovative methods
that reflect state-of-the-art technology. The methods have been reliable in use under
stringent production conditions for a number of years. In particular, it is ideal for
increasing the productivity and saving material. It is not only suitable for the sections
in the automotive and shipbuilding industries but also for plate packing of sections and
production of large diameter pipes.
Gräbener Maschinentechnik GmbH & Co KG
– Germany
Fax
: +49 2737 989 110
:
graebmasch@graebener-group.comWebsite
:
www.graebener-group.com
Gräbener’s TWP
®
plant (TWP = tailor welded plates)
Range of seamless steel
and LSAW pipe
Established in 1994, Shanghai Yueyuechao
Steel Tube Group is a manufacturer of seam-
less steel pipe, seamless square/rectangle
steel pipe, and large OD LSAW pipe.
Shanghai Yueyuechao is the manufacturer of a
range of pipe products
The range of the company’s LSAW pipe is
Ø 356-1,422mm x 12-60mm, according to
the quality standards of API, ASTM, BS,
ISO, DNV and JIS. The range of cold drawn
seamless steel tube is from Ø
6-426mm
x 1-20mm, while the hot expanded tube
specification range is from Ø
168-630mm x
4-30mm.
The company’s range of seamless steel
tubes is designed for construction, fluid
conveyance, high/medium/low pressure
boilers, petroleum cracking, and high-
pressure fertilizer equipment. The products
are also utilized as dew point anti-erosion
steel tubes, high carbon and chrome
bearing steel tubes, cold drawn or cold-
rolled precision steel tubes, square/
rectangle seamless steel tubes and various
alloy steel tubes (API, ASTM, DIN, EN).
In addition to China, the company’s pipes
are exported to USA, Germany, Canada,
Spain, New Zealand, and Korea.
Shanghai Yueyuechao Steel Tube
(Group)
– China
Fax
: +86 21 66788087
:
yycit@yyc88.cnWebsite
:
www.yyc88.comLoeco, Germany, is involved in the
engineering, manufacture and worldwide
supply of industrial plants. The company
places special emphasis on environmental
precautions and efficient automation for
high-speed production and protective zinc-
coating of top-quality tube and pipe.
Loeco’s state-of-the-art automatic pipe
pickling and galvanizing plant has just
started production at Tata Steel Tubes
Division in Jamshedpur, India. Following
modernization of the first galvanizing bath
at Tata Steel, Loeco has now supplied a
second galvanizing bath, equipped with a
double-dip and extracting system.
Loeco has also integrated a new pickling
line – completely housed-in – with automatic
one-by-one transport of the pipes through
degreasing, acid, flux and drying/preheating,
to feed the two galvanizing baths.
Tata Steel’s new galvanizing plant has been
designed for round pipes from ½" to 4", as
well as square and rectangular profiles.
The plant has a production capacity of
100,000t/year.
To save the environment and ensure worker
health and safety, acid and zinc fume
suction and cleaning are integrated in the
plant as well as a flux preparation.
In recent years, Loeco has also successfully
modernized older pipe-galvanizing plants
by installing new handling systems on
existing furnaces. This fully automatic pipe
Next generation zinc-coating plant
handling system has pipe dipping screws,
pipe positioning and a lifting device. It also
comes with a pipe extracting machine with
excess-zinc-blowing and water quenching
and blowing, and can be designed to fit
most existing galvanizing furnaces.
Loeco GmbH & Co KG
– Germany
Fax
: +49 208 5898124
:
loeco@t-online.deWebsite
:
www.loeco.de