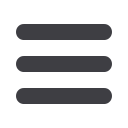

S
eptember
2008
www.read-tpt.com48
T
echnology
U
pdate
›
ASD Automation und Sondermaschinenbau
GmbH, Germany, is the specialized
manufacturer and supplier of stamping and
embossing machines for marking a variety
of steel and metal parts. The company
offers a new generation of ULU-standard-
universal machines that claims to cover
around 90 per cent of user requirements.
With largely identical parts and modules,
these machines remain universal while
allowing further optimization. They have
additional functional units and parts,
allowing the machine to provide extra fields
of application and optimal adaptation of
the machine(s) to the product sizes. This
increases the efficiency of the production
throughput, reduces cost and boosts
productivity.
A highlight of the ASD capability is the
innovative roll-on embossing machine
range – branded ULU 80/170 – which is
universal, longitudinal and circumferential.
This machine provides a range of functions
for state-of-the-art embossing and marking
technology.
The ULU 80/170 offers longitudinal
(continuous) roll-on embossing for strips,
coils, metal sheet, pipe (plastic/metal),
thin-wall pipe, and sections of all kinds
(eg round, square, hexagon, oval, flat,
formed). Embossing is carried out along the
longitudinal axis, with specified distances,
to an accuracy of approximately 0.1mm.
Full and variable feed-through speeds are
possible, up to approximately 200m/min.
The machines can also be used for round
(circumferential) roll-on embossing of short
and long pipes, pipe fittings and one-sided
form bent pipes.
The roll-on embossing machines are
universal, enabling marking of a variety
of cylindrical parts on the circumference,
multiform, and in one or more lines, or with
reductions. Marking can also be carried out
on coils and long metal sheets in varying
widths on cut-to-length machines (eg they
are ideal for steel service centres).
The machine also enables fully automatic
feeding and conveying of large throughputs.
This can be applied to marking on the
circumference in single or more lines, eg
for fittings, sockets, hose casings, ferrules
and threaded bushes and other mass-
produced short round parts and thin-wall
products.
The feeding devices can be modified and
adjusted accordingly. Each feeding and
unloading stroke of a/m mass-produced
parts occurs without any compressed air
consumption (presently the most expensive
energy source). Consequently, there is a
constant guarantee of high efficiency –
particularly in cases of larger batches.
These four capabilities (longitudinal,
circumferential, universal and automatic)
equate to four machines in one. They lead
to high flexibility and variety, resulting in
numerous and versatile possibilities of
application. This enables rapid set up
and accommodation of products up to Ø
80/170mm. With a modular extension,
the machine can even be used for
circumferential marking of flange rings and
pipe sections up to around Ø 1,000mm.
With rapid change of embossing types, two
sizes are available as standard machines,
enabling optimal adaptation to different
products. The machines have many
configurations, ensuring versatile and
flexible modular systems with an upwards
compatible design. Upgrading can be
carried out as required, together with future
retrofitting.
Accessories include special embossing
types for thin-wall pipes, flexible pin designs,
and various cleaning devices. Round
profiles can also be marked longitudinally
Latest vision system software for tube production
Xiris Automation Inc, Canada, has developed a software package for vision systems
that it plans to introduce to the tube industry. The software, Laservision
™
, is at the heart
of the company’s newest solution. The system runs on Windows
®
2000/XP using VB or
Visual C++
®
.
Laservision is a 3D machine vision software package designed for tube applications
in which highly accurate, repetitive measurements are required. The software can
function as a precision measurement tool, a locating system, a feature presence/
absence inspection system, or pattern matching system.
When integrated with the appropriate hardware, it can perform machine vision tasks
on the production line, providing 100 per cent inspection of high-speed production
volumes. This tool set will also be geared for a number of OEM partners as part of their
products.
Xiris has used this software to develop a vision system, which is currently in beta
testing, to evaluate the V angle, mismatch, edge presentation during forming in welded
tube production. The company plans to finish beta testing and have the final product
ready for October 2008.
Says Mr Pierre Huot, vice president at Xiris,
“It has by no means been an easy
endeavor to clear the technical hurdles to meet the market needs; nevertheless we are
quite excited about the value Xiris and the platform will bring to the industry.”
Xiris Automation is a specialist in optical quality control, and offers expertise in ‘in focus’
measuring.
Xiris Automation Inc
– Canada
Fax
: +1 905 331 6661 •
:
phuot@xiris.com•
Website
:
www.xiris.com/tube
ASD’s high performance tube pass unwind press
(Rdpm 5-160)
Specialized machines for
permanent product embossing