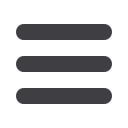

Wire & Cable ASIA – September/October 2007
105
i
l
11
The cable industry also was aware that it would need to
develop its own tests to properly assess the performance
of its products. Although this early development led to a
series of tests that could be said to lack integration, the
approach when taken as a whole still sits well with current
thinking.
Another important consideration was that large scale
tests should be developed wherever relevant so as to
assess performance of the total product in something
approaching an “as installed” condition. The international
work concentrated on the development of test methods
so that these could be adopted as an “add on” to product
standards such that the widest possible levels of fire
performance could be achieved across the full range of
product types.
Current Situation
The relevant IEC test standards have remained largely
unchanged over recent years but have been subject
to ongoing refinement
(5,6,7,8)
. For example, IEC 332-3
has developed into a multipart standard with each part
covering a different installation condition or time of
exposure to the fire source.
The principles established in the early development of
these standards still serve cable manufacturers and users
well and the IEC standards are adopted in many countries.
Based on the use of these tests, one can find in the market
various types of cables. Reduced flame propagation
(RP) cables which when installed in vertical bunches
in accordance with the recommended procedures do
not propagate fire more than a limited distance from
the source. Such cables have been well established in
the market since the 1970s for cabling in areas where,
because of installation conditions, eg vertically mounted
bunched cables, the risk of propagation of fire is high.
They are tested to the various parts of IEC60332-3.
Low smoke cables which have limits on smoke evolution
when assessed in the 3m cube smoke chamber with
performance limits chosen to give visibility over 10m
distance. They were introduced because cables containing
conventional sheathing materials based on PVC were seen
to give off large amounts of dense smoke when affected
by fire.
Such cables have been manufactured since the 1970s,
but it was not until advances were made in cable making
material technology in the 1980s that cost effective
designs became widely available on the market. They are
tested to IEC61034-2.
Generally cables of this type also combine the properties
of low corrosive gas emission and are manufactured using
“halogen free” materials.
Low corrosive gas emission cables which have limits
on acid and corrosive gas emission when assessed
by burning samples of materials in a bench tube
furnace. They were first introduced when users began
to raise concern over the large amounts of acid gas
emissions from burning reduced propagation PVC
cables. This corrosive and irritant gas had been seen
to have devastating effects on electrical panels and
instrumentation exposed to cable fire effluent
(9,10)
.
❍
❍
Figure 2
: prEN50399 apparatus
❍
❍
Figure 3
: Typical SPR and HHR curves