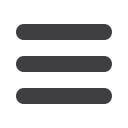

21
CONSTRUCTION WORLD
SEPTEMBER
2017
Installation of Franki Piles.
“The varying ground conditions with old
rock-filled docks and piers and the high-
water table as described above present a
significant challenge.”
Some of the existing live services which
required special attention to maintain
supply to neighbours.
is effected rapidly using the ‘Down The Hole Hammer’ (DTH)
percussion drilling technique. As with CFA, noise levels are low
and vibration limited. Schultz says that the foundation piles were
designed with flexibility in mind to meet the varying and sometimes
unpredictable ground conditions. Three pile types were used: the
Franki Driven Cast-in-Situ piles, Temporary Cased Augers and
Oscillator piles with individual load bearing capacities from 2 300 kN
to 10 000 kN.
To say that the Franki Pile is the most well-known
piling system in southern Africa is certainly no
exaggeration. Developed circa 70 years ago it is still
one of the most popular pile types in this region. Its
main feature is the large base formed at the toe of
the pile and, in forming it, the end-bearing area is
considerably increased.
It is generally a very economical system, has an
extensive range of pile sizes and, like the other piling
systems used on The Yacht Club site, its noise levels are
relatively low.
Another significant challenge on this project was
the very demanding schedule. “This meant that the
works not only had to be very carefully planned but also
executed to perfection,” says Schultz.
He explains that AMDEC required a phased handover
to the main building contractor so that the critical-
path tower cores and basement sections could be
started whilst Franki were still busy on site. “We started
operations during the latter half of 2016 and completed
everything on time and within budget by mid-March
2017,” he says.
Schultz paid tribute to Franki’s client, AMDEC, and to
bulk earthworks contractor, Ross Demolition. “To have
successfully completed this project on time we needed
it to run like clockwork. This was facilitated by these two
professional companies which pulled out all the stops to
ensure that we could do it,” Schultz concluded.