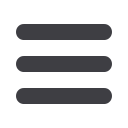

Paper 2: Why embrace the concept of the Safety Requirements Specification?
Institute of Measurement and Control – Functional Safety 2016
1
Paper: 2
Why embrace the concept of the Safety Requirements
Specification?
Russell Cockman
Functional Safety Consultant, Europe – Emerson Process Management
Abstract
Process safety and functional safety have the same fundamental goal, to reduce the
risk to people and the environment posed by intrinsically hazardous processes. The
safety instrumented system (SIS) is only there because the process risk is not ALARP
without it. The success of a safety instrumented function (SIF) is entirely dependent on
it doing the right thing at the right time in the right way. Given this common goal it is
strange that there is often such a disconnect between them throughout their lifecycle.
This disconnect starts at the beginning of the safety lifecycle. How many SIS
specifications do you see with no mention of the process being protected at all? It is no
wonder that specifications are the source of so much failure, as we cannot tell from the
specification what exactly is the design intent of each requirement, we just go on
assuming that the requirement is right. If you look at the suggested SRS content in
IEC61511-1 you can see that requirements of the process dominate. However, the
importance and significant benefits of the SRS are not appreciated.
Based on recent experiences of the author in helping customers prepare their SRS, we
will explore the benefits in doing so and the change in approach required to get the
most from this activity. We will look at how to make the SRS a valuable tool rather than
just another document. It will give examples of where a dedicated SRS activity can
yield positive benefits to the overall safety achieved.
Introduction
Properly designed Safety Instrumented Systems (SIS) are made up of highly
reliable components with a Probability of (random) Failure which is very low
indeed; low enough such that the risk reduction provided by these Safety
Instrumented Systems brings down the risk in the processes we operate to a
tolerable or broadly acceptable level. However, choosing reliable equipment is
only part of the story. We know from experience that failures of protection
systems can come from a variety of places with many traceable to human error
at some point in the history of the process affected. Such failures are referred
to as systematic Failures and are managed by following performance based
standards such as IEC61511.
Why process industries are safe
Decades of experience and expert input has led to the development of many
prescriptive standards, industry best practices and comprehensive company
procedures. Over the life of a hazardous process the automation system goes
through many phases. During each phase various factors significantly impact
the probability that the process and its protection systems will be safe.