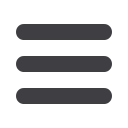

Technical article
September 2017
70
www.read-eurowire.comThe existence of several protective areas
means that activities can be performed
by the operator in one of the areas while
automatic movements are still taking
place in the other. When such a sub-area
is opened, the speed there is automatically
reduced to a safe level.
“In
addition,
due
to
the
spatial
arrangement of the consoles, a sufficient
distance to the moving machine parts
and the strip is ensured by design”, said
Mr Lüdecke. The normal length of time
until standstill is 12 seconds, but this can
be reduced to six seconds or, in the case
of emergency, even to three seconds if
required.
From the operator’s point of view, the
material runs from left to right through
the installation at a speed of up to 300m/
min. The individual process steps are
visualised by means of overview and
detailed images. The operator can perform
input directly via buttons and data fields
in the images or via pop-up windows. The
axle positions typical for the materials
can be stored as individual data sets with
alphanumeric names in a database.
Customer-specific order management
can also be integrated into the system.
Connection to the company’s network
ensures that the operator can access
the current production plan at all times.
During a cassette change, the system
recognises by means of an identification
system which cassette is currently
installed.
Manual,
time-consuming
readjustment is no longer necessary. By
means of further automatic systems, for
example in the form of an automatic coil
and spool transport, parallel activities can
be performed. As a result, what previously
took two operators to do can now be
undertaken by a single employee.
A feed-in system developed by B+S also
contributes to economic efficiency and
convenience. In this case, the strip to be
processed is mounted as usual in the
form of a coil onto the decoiler. Manual
feed, however, is not necessary. Instead,
the beginning of the strip is clamped in a
clamping bar at the beginning of the line
and pulled through to the outfeed at a
speed of 10 to 15m/min. This means that
no pilot strip is required, and welding or
the need for guide plates is eliminated.
Initial winding on the recoiler also takes
place automatically with a belt wrapper.
“The productivity of the line is increased,
since the actual processing can be started
quickly and efficiently,” summed up the
technical manager.
To ensure that the strip is wound up neatly
at the end, the decoiler and recoiler are
also each equipped with a strip edge
controller.
The reels, each weighing six tons, stand
on linear guideways that are pre-loaded,
free of play and mounted on anti-friction
bearings. Together with the edge
detection and position control, the reels
ensure precise unwinding and winding via
a servo-hydraulically controlled hydraulic
cylinder.
n
Burghardt + Schmidt GmbH
Raiffeisenstraße 24, 75196 Remchingen,
Germany
Tel
:
+49 7232 36610Fax
:
+49 7232 3661 65:
info@b-s-germany.deWebsite
:
www.b-s-germany.de