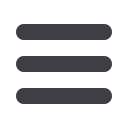

26
Mechanical Technology — July 2015
⎪
Hydraulic and pneumatic systems
⎪
“
A
erzen Airgas offers highly-
efficient equipment that
can assist operations in
considerably reducing
energy bills,” begins Stubel, admitting,
however, that the initial purchasing cost
is a dominant factor in the decision mak-
ing process.
“This makes the introduction of more
expensive but efficient equipment chal-
lenging. Understandably, buying equip-
ment at the lowest price makes financial
sense, but the misconception lies in the
fact that cost saving decisions are based
primarily on short-term financial goals,”
he says.
Stubel points out that purchasing
Rising electricity costs and unreliable supply from the national grid are prompting
industrial operations to seek more energy-efficient
equipment. However, the major challenge in South
Africa still lies in the market’s reluctance to focus
on long-term investment, by spending more on the
initial purchase price to ensure future savings, according
to Aerzen Airgas marketing co-ordinator Andreas Stubel (left).
The Delta Hybrid is
designed to be an optimised com-
bination between a blower and screw
compressor, and makes use of a patented
twisted rotor profile.
In conjunction with new machine sales, Aerzen Airgas offers numerous after sales services including field
service, repairs and overhauls to the entire range of Aerzen blowers and compressors.
Compressor investments, long-term
standard or cheaper equipment does not
save money, and may in fact cost more
in energy consumption and maintenance
in the long run. “Bearing this in mind,
Aerzen Airgas offers the local market the
Aerzen Delta Hybrid rotary lobe compres-
sor, an oil-free air conveying alternative
to standard roots blowers,” he continues.
The Delta Hybrid is designed to be
an optimised combination between a
blower and screw compressor, and makes
use of a patented twisted rotor profile. It
is designed for a variety of applications
where air and neutral gases must be
conveyed oil-free. These include; waste-
water treatment plants, the chemical
industry, power plant technology and for
the pneumatic transport of powder and
granulate goods.
The Delta Hybrid is available in four
models: L, S, H and E. The L model has
been designed for pressure ranges of up to
800 mBar; the S model for 1 000 mBar
and the H model for pressures of up to
1 500 mBar at sea level. The E model
is a vacuum machine with a maximum
negative pressure of -700 mBar. The
Delta Hybrid is effectively an in-between
solution, as it crosses the pressure range
between roots blowers and low-pressure
screw compressors.
“The Delta Hybrid is a compres-
sor designed from the bottom up with
energy-efficiency in mind. As a result, it
is up to 15% more energy-efficient when
compared to standard positive displace-
ment blowers. It has an optimised fluidic
design of inlet and discharge ports to
provide for ideal flow conditions and
reduced slippage,” Stubel explains.
The inlet air is sucked in on the cold
side of the unit and a specially designed
discharge silencer increases the compres-
sion efficiency. What’s more, the belt-
driven Delta Hybrid offers the significant
advantage of exact sizing for customer
requirements.
For demonstration purposes, an
Aerzen Delta Hybrid D 24 S was tested
alongside a standard positive displace-
ment blower, both fitted with 37 kW
IE2 motors. Both machines were con-
figured to produce a system pressure of
900 mBar and an intake volume flow
of 1 000 m³/h at sea level. The Delta
Hybrid consumed 27,5 kW to produce
these figures, while the blower consumes
32,3 kW for the same performance. “On
average, therefore, the Aerzen Delta
Hybrid is 14% more efficient than the