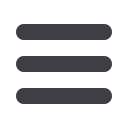

Mechanical Technology — July 2015
21
⎪
Computer-aided engineering
⎪
While developers will typically start with
CAD, then go to engineering analysis
based on the 3D CAD model and then
onto manufacturing, we advise a process
change involving these three questions
being addressed in advance of CAD.
On the material side, composites,
aluminium or titanium are typically used
as substitute options in lightweighting ex-
ercises. Any change in material, however,
must come with an associated change
in the topology of the new component.
“The cornerstone of solidThinking
Inspire involves automatic topology
optimisation,” Smith says, opening the
software to display how solidThinking
works. “At its starting point, a part is
sketched using primitive solids (cubes,
cylinders, etc.), or an existing part can
be imported and de-featured to define the
design space. Then the fasteners, joints
and boundary contact points are defined,
before the required materials and external
structural loads are assigned.”
Once the basic shape, engineering
materials and specifications have been
assigned, solidThinking begins to gener-
ate an ideal shape. “Embedded in the
analysis tools are bio-mimicry philoso-
phies. Bones grow stronger along load-
paths where they need to. In the same
way, the geometry of a part can have
ribs, struts or thickening added where it
is needed and removed where it is not
needed. The topology of the part can,
therefore be quickly and automatically
established before doing any detailed
design,” he reiterates.
Once complete, the part performance
is verified before the resulting geometry
is smoothed using Evolve, the free-form
design software from solidThinking, or
the geometry can be exported into a CAD
package for refinement and integration.
Evolve makes use of NURBS (non-
uniform rational basis splines) – com-
monly used in computer graphics for
generating and representing curves and
surfaces. “NURBS allows for flexibility
and are widely used in free-form design
and clay modelling tools,” he explains.
Underpinning solidThinking’s optimi-
sation capability is Altair’s OptiStruct
®
structural optimisation technology which
is available under HyperWorks licens-
ing for more advanced simulation and
analysis, if required.
On the manufacturing side, additional
options allow part topology optimisation
that suits the preferred manufacturing
method. “We are particularly strong on
3D printing or additive manufacturing.
Designs can be exported for pre-3D
print processing to several packages
developed by the major 3D printer manu-
facturers, for example 3-maticSTL from
Materialise,” Smith continues, adding,
“3D part printing allows a high degree
of complexity and flexibility in terms part
geometry”.
But manufacturing shape controls for
processes such as casting, moulding or
stamping are also embedded into the op-
timisation constraints. If being extruded,
for example, solidThinking generates
constant cross-section topologies based
on the extrusion direction.
In spite of the power of the solidThink-
ing Inspire, “the software is very easy to
learn” and it is compatible with existing
CAD tools, such as Creo Parametric.
“Typical training for a design engineer can
be done in a single day,” Smith assures.
Niche successes include: the sup-
porting struts for satellites, a simple
basic design that is then lightweighted
to optimise dynamic performance; the
hinges on aircraft doors, which resulted
in a 64% weight saving; and advanced
bicycle frames.
“Not only is Inspire successful in the
aerospace industry, but also automotive
manufacturers, such as Daimler AG, are
officially certifying solidThinking Inspire
for company wide use,” Smith reports.
With the Daimler certification, all
design engineers within the car and
truck development departments of the
company may now use solidThinking
Inspire within their projects, giving them
an opportunity to create efficient struc-
tures with minimum weight. This works
for components, assemblies, and entire
systems. Design engineers may also use
solidThinking Inspire to apply a required
stiffness on a component where needed,
helping to avoid undesired vibrations and
contributing to overall vehicle comfort
and quality.
Standalone licences of solidThinking
products are available through the lo-
cal channel partners or as tools within
Altair’s HyperWorks suite of simulation
software.