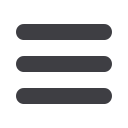

M
ay
2008
www.read-tpt.com58
T
echnology
U
pdate
›
Zumbach, Switzerland, offers a complete
line of measuring and monitoring
instruments. In the steel and metal
industry, the company’s systems are used
in the manufacture of hot and cold rolled
products and in cold processes for semi-
finished products. Typical areas of system
useage are hot rolling mills for wire steel
rod, profiles and seamless pipes, welded
pipe manufacture, test stands (NDT), and
cold processes such as peeling, grinding,
straightening and polishing.
The company’s Steelmaster gauges and
systems are designed to fulfil market
requirements such as closer tolerances,
zero fault, 100 per cent quality control,
higher productivity, faster start-up, less
downtime and less manpower.
The Steelmaster processor is the ‘brain’ of
the system, as it processes the measuring
data, communicates with the plant
network and provides the operator with
self-explanatory displays and key data.
The process transparency is dramatically
improved, especially if multiple measuring
heads are installed.
SMO oscillating gauges for round and non-
round products feature up to six measuring
axes, seamless 360° coverage, no blind
zones, and measurement independent of
twist. With an increased number of axes,
more data can be captured at the same
time, and the measurement cycle per
profile is shorter. SMO gauges can also
be operated in static mode, in selectable
orientation.
SMS static gauges are suitable for round
products, and feature up to six fixed
axes, no moving parts, compact design,
practically no maintenance, fast measuring
rate (1,000/s in longitudinal direction), and
short measuring distances.
Advantages of the Steelmaster gauges
include easy integration, dependable
operation, up to 6,000 measurements per
second (1,000 per scanner), distributed
intelligence, one single (fibre optic) cable
between LPO and CPO, compact industrial
PC with highest working reliability, highly
developed software, and sophisticated
mechanics and protection system.
ODAC
®
laser scanners with latest optical
and laser technology are the ‘heart’ of
the Steelmaster gauges. Zumbach offers
ODAC models with measuring fields from
15mm (0.59") to 500mm (19.68"), and
larger models upon request. The scanners
are accurate and permanently calibrated,
with high resolution, high measuring rates
(up to 1,000/s), and high immunity to dirt.
Zumbach has developed a novel
measurement method called FPS (Full
Profile Synthesis, patent pending), ideal
for special geometries of polygonal shape
aberrations (generated by 3-roll blocks),
specific profiles and asymmetrical shapes.
Scanning a multitude of shadow edges
around the entire periphery captures
the product shape. This is achieved with
several ODAC measuring heads, scanning
synchronously with high accuracy.
This FPS method, based on special
algorithms, generates a complete profile
synthesis (contour). This profile makes
it possible to derive data, such as out of
round, reference centres and other key
elements, used for the adjustment of the
rolls. Oscillating SMO systems are able
to capture more data, allowing for precise
profile measurements. Even in the case
of varying twist, or if the extreme points
have not been captured by any scans,
this method provides exact values of the
minimum, the maximum, out of round
condition and the derived data.
Steelmaster software offers all functions
needed for round products. Additional
software modules are available for non-
round products, including squares,
hexagonals, flats, rebar, and polygonal
shape deviations (3-roll blocks). Optional
modules are also available for additional
functions such as network communication,
data archiving, remote workstations, and
SPS statistics.
The hardware and software for all
Steelmaster versions can be upgraded
at any time. The main data, such as
measuring rate, accuracy, measuring para-
meters and all optional upgrades are the
same. High flexibility allows for individual
configuration of the screens with section
and trend displays (numeric and graphic),
printing protocols, and statistics. Several
programmable access levels and passwords
allow for optimum use and data safety.
New sensor system for Novaflux flux leakage system
Prüftechnik NDT GmbH, Germany, has released a new sensor system for its recently
introduced Novaflux flux leakage testing system. The RFL65 rotating unit is used for
the highly sensitive inspection of black and bright steel bars and seamless tubes with
diameters from 5 to 65mm.
The new option broadens the Novaflux
portfolio, which initially set out with
RFL140 for diameters from 10 to 140mm.
Novaflux is able to find longitudinal
defects of a depth greater than 0.1mm
and handle high production speeds of
up to 3m/s. The system is operated via
a user-friendly touchscreen. A detailed
report of the test results permits further
processing of defective yet repairable
bars and thus increases the yield.
Novaflux can also be operated together
with sensor systems of other vendors.
As a specialist in eddy current inspection
systems for the semi-finished products
industry, Prüftechnik provides the industry with a wide portfolio of testing equipment
for reliable quality control. Eddycheck
®
and Novaflux test equipment is used in a wide
variety of different production areas, for process monitoring and for the final inspection
of tubes, bars and wire. Eddy current testing meets an extensive range of international
standards including ASTM, API, BS, JIS, ETTC, ENEL, DIN and SEP.
Prüftechnik NDT GmbH – Germany
Fax
: +49 89 967990
:
info@pruftechnik.com•
Website
:
www.pruftechnik.com
Prüftechnik’s RFL65 rotating unit
Non-contact in-line dimension measurement
in the steel industry