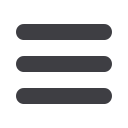

ENERGY
“P
iston compressors have always presented a compelling offer
in terms of robustness, low maintenance and energy effi-
ciency but this strong performance always came with high
noise levels and few control options,” says Atlas Copco Compressor
Technique’s Business Line Manager - Industrial Air, Charl Ackerman.
The Atlas Copco LZ eliminates this trade-off; it is the most complete
oil-free piston compressor on the market, meeting all clean com-
pressed air needs.” Ackerman points out that as energy use consti-
tutes the highest cost of running a compressor, it is absolutely essential
that a compressor operates as lean as possible. “Given the protracted
power supply crises facing South Africa, reducing energy consumption
has become even more critical. Our LZ compressor features a number
of built in innovations that dramatically reduce energy consumption.
For example, the direct-drive and start-stop technology eliminate waste
during the unload cycle while the one-bearing motor reduces mechan-
ical friction.”
Even after filtering, the complete removal of all oil vapours, aerosols and
other contaminants from oil-injected compressed air can never be 100 %
guaranteed. Thanks to Atlas Copco’s innovative oil-free technology, the LZ
compressor features an ISO 8573-1 Class 0 pump that produces TÜV-certi-
fied 100 % clean air.When it comes to reliability and low operational costs,
there are few compressors that can match the LZ range which boasts an
impressive operation life time of 20 000 hours. A number of factors con-
tribute to this extreme reliability including the use of quality components in
manufacture such as patented steel inlet/outlet pump valves. The fact that
the LZ does not use any oil delivers across-the-board savings including lower
maintenance costs and reduced service interruptions all of which have a
direct and positive effect on uptime and ultimately productivity.
“Lubricated compressors operate up to 20% of their running time to cool-
down mode,” notes Ackerman. “The oil-free technology and internal cooling
fan system of the LZ offers 100% duty cycle for uninterrupted service.” An-
other advantage is that unlike lubricated compressors the oil-free LZ does
not require additional filtration equipment. The use of a canopy and sound-at-
tenuating fabrication materials result in low noise levels of up to 67 dB(A).
This silent performance which was previously unattainable for an oil-free
piston compressor, makes the LZ suitable for sound sensitive environments
and optimises a healthy and comfortable working environment.
The LZ’s advanced built-in easy-to-use MK 5 one-touch electronic control-
ler optimises compressor performance and reliability with integrated saver
cycles, smart algorithm for cooling and duty cycle, a maintenance schedule,
pressure temperature and life time monitoring, etc. The LZ also presents a
high performance cost effective foundation for the Atlas Copco on-site ni-
trogen generation system. This system which combines a compressor such
as the LZ with a nitrogen generator ensures a dependable supply of purified
nitrogen gas with purities of up to 99,999%. Ackerman explains that Atlas
Copco’s latest NGP+ on-site nitrogen generator can simply be plugged into
an existing compressed air network to produce nitrogen which is an inert
gas replacement for air to prevent oxidation and preserve the freshness of
wine and packaged foods. Nitrogen is also used in laser cutting, chemical
manufacture and the production of electronic parts to prevent moisture build
up. “The LZ’s compact footprint and the fact that it does not compromise the
adsorbent of the nitrogen generator, makes it highly suited to the nitrogen
generation system,” concludes Ackerman.
b
ATLAS COPCO LZ OIL-FREE
COMPRESSOR
delivers absolutely clean air
with maximum efficiency
CAPITAL EQUIPMENT NEWS
JUNE 2015
31