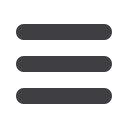

Technical article
January 2015
43
www.read-eurowire.combroadened, and Raman scattering intensity
near the 1,560cm
-1
region is pronounced.
Broadening of the diamond band is a
result of decreasing the grain size to the
nanometer scale, and the presence of
scattering intensity at 1,560cm
-1
is due to
increasing graphite-like or amorphous
carbon sp
2
-bonded components at the
grain boundaries in films. Raman scattering
is 50~60 times higher for sp
2
-bonded
carbon
compared
to
sp
3
-bonded
carbon, hence the diamond component
dominates in films.
The Raman spectrum of the nano-
crystalline diamond film in
Figure 3
can
be regarded as the representation of the
surface of the composite diamond film
because the Raman spectrum reveals the
structure of the top layer of the film.
The surface profiles of conventional
multi-crystalline coating and nanocrystal-
line diamond composite coating were
tested with the same thickness at five
sampling sites with surface profilometer,
and the results of the surface roughness
(Ra) were 309.64nm and 104.71nm,
respectively. By comparison, Ra of the
nanocrystalline
diamond
composite
coating could reach 30nm or even lower
after mechanical polishing.
According to the characterisation and
analysis, the nanocrystalline diamond
coating has a smooth surface with a
grain size of about 50nm, which is much
smaller than conventional multi-crystalline
diamond coatings. This is advantageous to
the surface polishing of diamond coatings.
Therefore, nanocrystalline diamond com-
posite coatings dies (nano-dies) can
easily be fabricated, see
Figure 4
(with die
casing), to meet the requirements of both
excellent wear resistance, very high finish
and low friction with aluminium.
4 Application tests
of nano-dies for
aluminiumwire
drawing
4.1 Conventional application
tests of nano-dies for
aluminiumwire drawing
We prepared nano-dies with various
specifications (bore diameter smaller
than 4mm) for aluminium wire drawing,
using the above nanocrystalline diamond
composite coatings technology and
subsequent polishing technology.
According
to
practical
aluminium
enamelled wire and aluminium wire
drawing
tests
performed
on
the
production lines of customers in China,
nanocrystalline
diamond
composite
coatings show very good adhesion
performance, wear resistance and much
lower surface friction. The nano-dies
showed a die life improvement by a
factor of about 10 to 25, when drawing
speed was about 15m/second, so it can
not only save cost of drawing die itself,
but also largely reduce change-over time
(only 4% to 10% of previous process) and
dramatically increase productivity. Because
the friction coefficient between diamond
coating of nano-dies and aluminium
conductor is so small (only about 0.09), use
of nano-dies can obviously improve the
surface finish of drawn products and avoid
aluminium galling on drawing dies.
The super wear resistance of the diamond
coating of nano-dies yields consistency of
wire diameter, saving raw metal material
up to 1~2%. Additionally, nano-dies are
welcomed in high-speed wire drawing
and they are highly applicable to environ-
mentally friendly ‘non-pickling’ wire
drawing processes.
4.2 Water lubricating application
perspective in Al wire and coaxial
cable/Al-plastics compound pipe
drawing process with nano-dies
There is another dominant advantage of
nano-dies studied in this paper. That is the
change of lubricating method with a most
attractive green element in addition to
direct cost savings.
Most production lines with TC dies use
oil-based lubricants to cool the dies and
decrease the friction in the reduction and
bearing zones of the die.
Another consideration is the finish of
aluminium products. TC dies need an
oil-based lubricant in order to achieve
a satisfactory surface finish. However,
oil-based lubricating systems also bring
lots of concerns.
For example, the cost of lubricants is
high, expensive accessory equipment
is required, and there is consumption
of oil resources (in oil-based lubricant
manufacturing processes).
Additionally, oil-based lubricants carry
pollutants into the workshop (smog,
chemical particles and microbes) and
there are great difficulties in recycling
aluminium scraps. For drawing customers,
the latter two factors are big problems,
especially aluminium scrap recycling.
A kind of water-based lubricating system
can be successfully introduced to replace
the conventional oil-based lubricating
system when using nano-dies for
producing coaxial cable and Al-plastics
compound pipe. This is becoming very
popular in Chinese production in recent
years
[5][6]
.
Success is the direct result of the unique
structure of sp
2
-bonded carbon in the
layer of nano-crystalline diamond coating
of nano-dies. It brings not only very low
friction in the interface with aluminium
(and with good self-lubricating, similar to
some graphite-like structures), but also
better wetting with lubricating film in
water-based lubricants (vs conventional
multi-crystalline coating).
Conventional
TC
dies
will
also
meet
difficulties
of
strong
oxide
etching
and
adhesive
wear
(to
form abrasive dust etc) when using
water-based systems. By contrast, the
process is completely worry-free when
using nano-dies because of the high
degree of chemical inertness and very low
wear rate of diamond coatings.
Figure 5
shows the water lubricating
application in the Al-plastics compound
pipe drawing process with nano-dies at
a customer’s plant in Zhejiang Province
of China and the final appearance of the
aluminium product.
Used in this manner, the customer saves
a large amount of cost of lubricating oil,
accessory thermostat cleaning equipment
and other processes, and significantly
reduces environmental pollution. The
Al-plastics compound pipes they produce
are more consistent, have a more accurate
diameter and a better finish than anything
previously achieved using TC dies and an
oil-based lubricating system.
The same story has been repeated
in multiple aluminium wire drawing
applications in China.
▲
▲
Figure 5
:
The water lubricating application in
Al-plastics compound pipe drawing process with
nano-dies and appearance of the aluminium
product
t