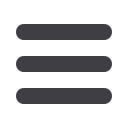

Schoder GmbH, Heinrich-Hertz-Strasse 19,
D-63225 Langen
Phone +49 (0) 61 03 59 71-0 · Fax +49 (0) 61 03 59 71-59
www.schoder.com·
info@schoder.comCoding tools from Schoder
code millions of parts worldwide
and also now engrave copper and
steel pipes, plastic pipes, cables and more.
Precisely incorporated pipe radii and rapidly
exchangeable embossed segments make
Schoder fast-running rollers flexible and cost-
effective.
For every pipe diameter and adapted for
every material. So that your products develop
their own identity and become unmistakably
unique.
Request a quote or visit our website.
IDENTIFICATION
FOR PIPES,CABLES
AND MORE
Anz_Schoder_Tube&Pipe 21.05.2007 10:09
Bandera, Italy, has supplied thermoplastic
pipe extrusion lines to two German
manufacturers. The complete extrusion line
will be used by one of the manufacturers
for the production of PP copolymer and
PPHD pipes for use in flue ducting. This
flue ducting is used for combustion and
discharge fumes of the condensate deriving
from gas boilers (in place of pipes made
from stainless steel or other traditional
materials).
The output of this line is 210kg/h
– significant considering that the line
processes thin pipes, cut in minimum
500mm long bars. The line consists of a
TR 65 AFTH L/D 1:32 extruder equipped
with a thermo-regulated feed-throat. A four-
component gravimetric dosing unit enables
the exact repetition of process recipes and
keeps pipe weight/metre constant, ensuring
very narrow dimensional tolerances.
Capable of producing pipes within a
diameter range of 32-160mm, the line
features a special vacuum calibrating
system. It also has an ultrasound thickness
control system equipped with eight fixed
sensors to check the thickness of the
pipes produced. The four belt haul-off unit
is designed with an increased belt contact
surface, to ensure that the thin pipes avoid
any deformation.
A planetary cut-off unit equipped with a
knife, without any residual swarf and with
automatically synchronised speed, allows
the user to obtain minimum length pipe
bars, even at the highest extrusion speed.
The high-performance belling machine can
form three sockets per time, on the basis
of the different diameters, and includes a
system for automatic ring seal fitting in the
different sockets.
An operator panel allows the control of
process parameters. These include the
gravimetric system, line flow, weight/metre,
and extruder running parameters (screw
velocity, temperatures, melt pressure etc).
It also calibrates tank parameters (vacuum
control, water temperature etc), monitors
the ultrasound thickness control system,
and also synchronises line velocity with
extrusion speed. It is equipped with a
modem for tele-assistance.
Costruzioni Meccaniche Luigi
Bandera SpA
– Italy
Fax
: +39 0331 680 206
:
lbandera@lbandera.comWebsite
:
www.luigibandera.comProduct launch for low noise
push-fit piping system
Designed to bring silent operations to
internal drainage, Wavin Plastics has
launched Osma SiTech – a new low noise
push-fit soil system. An easy-fix push-fit
system, SiTech is made from a mineral-
filled polypropylene, which has the effect of
increasing pipe density.
Higher pipe density means that it only
needs to be encased in 25mm of mineral
wool wrap where contact between the
pipe and the building structure cannot
be avoided. Consequently, it cuts down
on installation time, wrapping and tooling
costs and can be installed by professional
plumbers rather than specialist fitters.
Specialist fitters are often required for cast
iron and HDPE systems.
OSMA SiTech has been independently
tested for sound reduction performance
and helps to achieve the higher acoustic
performance standards in buildings as
required by the UK’s Building Regulations
Part E 2003. The OSMA SiTech system is
available with acoustic fittings and pipe in
the standard 110mm size.
Wavin Plastics
– UK
Fax
: +44 1249 443 286
Website
:
www.wavin.comThermoplastic extrusion lines for PP copolymer
and PPHD pipes
fi
Bandera’s TR 65 AFT-H extruder
›
The line includes a vacuum calibrating system
J
uly
/A
ugust
2007
P
lastic &
C
omposite
T
ube:
P
roducts &
M
anufacture
101