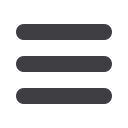

19
I
n South Africa, providing social,
Gap, Flisp and affordable housing
remains a major challenge. Sev-
eral thirdworld governments have at-
tempted to address the issue through
housing policies or programs offering
service sites and housing subsidies.
The reality is that most developing
countries do not have adequate capi-
tal resources to build conventional
housing. The South African govern-
ment’s goal is to create sustainable
human settlement developments
that engenders a sense of pride and
advances the upliftment of the entire
community.
Statistically over 50% of the
world’s population already reside
in urban areas. The impact of this is
particularly visible around South Af-
rica’s cities with informal settlements
adding to the urban sprawl.
Most settlements still comprise
of poor housing structures that are
often damaged during inclement
weather and have few utilities, com-
munity facilities, or proper roads.
Innovative building system
developer, André Esterhuizen,
established Stumbelbloc al-
most six years ago to provide
a cost efficient IBT system. The
interlocking innovative building
technology could offer a quick,
efficient, building solution in the
rural, low and middle income resi-
dential market.
The concrete building blocks
are produced from plastic moulds.
The interlocking building blocks are
filled with a mortar mix and left to
dry, creating perfectly formed con-
crete blocks. The strong, fast and
cost efficient construction method
has been approved by the National
Home Builders Registration Council.
For example a 16 m x 2 m wall
can be built from foundations in
40minutes and a small house includ-
ing roof and foundations, within
three days. The blocks can be pro-
duced and erected using unskilled
labour. This provides previously
disadvantaged people with employ-
ment opportunities. The innovative
building blocks can be produced
with a spade (to mix cement), trowel
and a rubber faced hammer. The
only raw materials needed include
cement, sand and stone, if required.
The product offers longevity, thermal
insulation, low life cycle costs and it
is environmentally friendly.
The system has been used to roll
out housing and there is a worldwide
patent and design right pending in re-
spect of the moulds and blocks.
■
Hebel wall withstands direct fire ex-
posure for up to six hours. A standard
100 mm thick Hebel wall can with-
stand temperatures for four hours.
Thermal insulation
The enhanced insulation perfor-
mance is five times that of brick of
the same thickness. The thermal
efficiency reduces the reliance on
heating and cooling appliances,
and provides up to 60% reduction in
energy costs.
Cost effective
The cost of Hebel panels and blocks
are only a part of life cycle costing of
a building.
When factors such as transpor-
tation, assembly and finishing, as
well as the energy efficiency, fire,
protection, maintenance, durability
and environmental properties are
considered, Hebel provides an eco-
nomical solution for the lifespan of
the building.
This includes savings of up to 15%
in structural costs (foundations and
structure) attributable to low mass
to strength ratio properties of AAC.
The reduced weight of walls: typi-
cal brick and mortar wall load is ap-
proximately 350 kg/m² - AAC blocks
wall load is approximately 90 kg/m².
Finishing
Conventional brickwork requires
plaster and skim coat for a perfectly
smooth finish whereas the extra
naturally smooth surface of Hebel
only requires a skim coat.
Sizes
The Hebel Block sizes are avail-
able in 600 x 250 x
100 mm (Mass = 10,2
kg) and 600 x 250
x 150 mm (Mass =
15,2 kg). The Hebel
Panel sizes range
from600mmwidth
and thicknesses of
100 mm and 150
mm, lengths span
2400 mm, 2700
mm and 3000
mm.
Everite Build-
ing Products is
currently sup-
p l y i n g A A C
products in
Angola for a
45 000 unit
project.
■
Solution
to housing
delivery
South Africa has a great need
for additional and alternative
methods of building techniques
and designs, while still providing
acceptable cost efficient housing
with a low environmental
footprint.