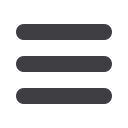

October/November 2016
O
con Brick has supplied clay
stock bricks for the multi-bil-
lion rand mixed-use Central
Square development, in Sandton’s
richest precinct. Shawn Herbst, Site
Agent for Mota-engil Construction
explains that Sandton has grown so
much over the past five years and civil
engineers have faced the challenges
of product storage spae on site and
the limited street widths. This makes
the need for stock delivery scheduling
a critical requirement.
Herbst explains, “With the narrow
roads of Morningside, Sandton, the
developers need to enable as much
traffic flow-through as possible with-
out causing congestion. Large trucks
loadedwith hundreds of brick pallets
needed to be offloaded quickly. Not
only did we have extremely tight
delivery times, limited storage space
as the Central Square development
grew, we had to move 24 000 clay
stock bricks up to the next level of
construction.” “We chose Ocon Brick
because we knew their clay stock
bricks to be of a high quality and
that the Ocon Brick team would be
available even at short notice, as we
micro-managedcrucial product deliv-
ery schedules to meet the restraints
at site. The Ocon Brick team met the
deadlines and delivered at 6am after
being ordered the previous day. It
is that kind of team work that we
sought and received for the Central
Square site.”
Ocon Brick supplied 5 208 000 for
the Central Square residential blocks,
“Construction commenced inDecem-
ber 2015 and is due for completion
mid-2017. With 52% of the project
already complete; there are a further
nine floors to be constructed and
17 000 m² of concrete parking decks
still to be completed,” says Ocon
Brick consultant, Lucas Steyn. “We
are fortunate that due to our large
manufacturing capability we are able
to hold sufficient stock at any given
point in time enabling us to meet
our customer’s specific time-critical
delivery requirements.”
■
Central Square
Shangase adds that the new Ma-
juba FET College state-of-the-art
college environment has set a new
standard for learning institutions.
The campus comprises a gatehouse,
administration offices, double-storey
blocks of 2 200m² each, an examcen-
tre, resource centre, student centre
and walkways. “Demand for educa-
tion facilities inDundee has increased
drastically over the past few years
with the growth in population and ris-
ing unemployment levels. To address
this imbalance, Majuba FET College
partnered with Endumeni Munici-
pality to establish Dundee campus
at Mpati. As part of the Umzinyathi
Community Education Project, En-
dumeni Municipality donated land to
Majuba FET College at the entrance
of Dundee for the establishment of
Dundee Technology Centre (DTC).
Tjaart van der Walt, Head Architect
of LVDWArchitects, explained that the
soil was particularly rocky.
“We opted for amore conventional
design in an effort to save on costs.
Brick construction with face brick-
work fulfilled all the requirements of
this college infrastructure. The neu-
tral colours of the face brick blended
in well with the surrounding environ-
ment,” explained Van der Walt.
The bricks were laid in a conven-
tional stretcher bond pattern while
the sturdy herringbone pattern was
selected for the pavers. Pattern work
was included in areas of the face brick
façade to express its African context.
T h e b r i c k w o r k i n c l u d e d
infrastructure
Bricks & Paving
combinations of Corobrik’s range
of Nebraska Travertine and Country
Classic Travertine face bricks for
the maintenance free facades, with
Champagne andBurgundy pavers be-
ing used to compliment the buildings
aesthetic and surrounds.
According to Shangase, “The
choice of colours and textures work
particularly well in the environment.
The life-time cost-saving benefits of
the face bricks is just one of themany
attributes that will serve this project
well into the future”.
■
Musa Shangase