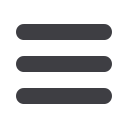

January
2014
101
Steel Plant Specialities
Article
surface quality is deteriorated due to pitting. Metallurgical
transformation during austenitising and subsequent quenching
may be non-uniform. Surface hardness and strength are also
lowered due to layer of scaling. Fatigue strength of heat
treated product is reduced. This is especially true in case of
automobile leaf springs.
Preventing oxidation and
decarburisation
Prevention of oxidation and decarburisation is not only better
than cure, it is profitable too. There are several ways to address
problems caused by the two harmful reactions. Decarburised
surface removal by machining operations after heat treatment,
copper plating of thickness upto 0.025mm prior to heat
treatment or change of heating media to molten salt bath
are some ideas. A number of protective atmospheres may
be introduced like liquid hydrocarbon, dissociated ammonia,
exothermic gas, nitrogen and endothermic gas. Fluidised bed
furnaces and vacuum furnaces have also proven to reduce
scaling.
Switching over to grades which do not require heat treatment
is possible in rare cases. However, most of the mentioned
solutions pose a number of problems or practical difficulties.
Availability of capital and human resource for using high-end
furnaces is a major issue. Many small heat treatment shops
cannot afford these solutions. Yet they are under mounting
pressure to prevent oxidation and decarburisation. Use
of protective anti-scale coating has proven to be a logical
solution to the problem of scaling and decarburisation.
Insights into use of protective
coating and its characteristics
Use of protective coating has been found beneficial and cost-
effective. An anti-scale coating is applied on components or
billets to be heated before charging them into the furnace.
This anti-scale coating acts as a barrier between oxygen and
metal.
Care is taken to apply a uniform, impervious layer of coating
on the component to be heated. Coating ensures prevention
of scaling and decarburisation. For exceptionally long heat
treatment cycles of 10 to 15 hours, the extent of scaling and
decarburisation mechanism is substantially reduced.
Anti-scale coating also reduces decarburisation on billets
and ingots during hot forging and hot rolling operations. Heat
transfer from heating media to metal is not affected due to
anti-scale coating.
No reaction with steel surface, no release of toxic fumes
during use or heat treatment or storage, non-hazardous and
economical implementation are other required characteristics
of the coating. Coated tools and components must be able to
be heat treated in air using a box type or bogie hearth; electric,
gas or oil fired furnace.
Benefits of anti-scale coating:
industrial case studies and
success stories
Table 1 shows the efficacy of the coating in an electric
furnace. Coating eliminates need of salt bath or controlled
atmosphere equipment in many cases. Considerable savings
in capital investment and operating costs are enabled by use
of anti-scale coating. Due to prevention of decarburisation,
uniform surface hardness is achieved. Rejected components
can be salvaged (figure 1). Large savings are possible when
plates of expensive alloy steel can be re-heat treated by using
the anti-scale coating.
Figure 2 explains the benefits of using coating during hot
forming and solution annealing of stainless steel pipe fittings.
Due to prevention of oxidation even in an ordinary oil fired
furnace, pickling time could be reduced by 75 per cent.
Buffing can be eliminated or minimised in many cases. In the
manufacturing process of shearing blades of expensive high
carbon, high chromium grade steel, grinding allowance is
substantially reduced when protective coating is used during
heat treatment. Some other distinct case studies are listed
below.
1. Prevention of quench cracks
Forgings like knuckle joints and crank shafts when heat
treated in furnaces of oxidising atmosphere are susceptible
Type of furnace used
: Box type, electric
Test coupon dimensions
: 300mm x 100mm x 10mm
Grade of steel
: AISI – 1010
Heat treatment cycle
: 1000°C / 4 hrs / air cool
% scale loss when not coated : 5.52
% scale loss when coated
: 0.70
Table 1
:
Efficacy of protective coating
Figure 1
: Ability to salvage the rejected components