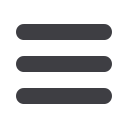

102
January 2014
Article
Steel Plant Specialities
to quench cracking. Quench cracks appear
when stresses generated during quenching are
higher than tensile strength of thin sections of
forgings and due to differential quench severity
at different areas. Chrome-moly grades of steel
are most susceptible to quench cracks, which
usually occur in the gear-end portion of the
crankshaft. By coating the gear-end with an anti-
scale coating, the cracking is prevented. (Image
1). By coating the gear-end with anti-scale
coating, cracking could be effectively prevented.
Reputed forgers of largest crank shafts in India
use this technique. (Endorsement 1).
2. Reduction in shot blasting time after heat treatment
Operations like shot blasting, grinding, acid pickling etc. do not
add value, but are expensive and time consuming procedures.
These operations are necessary to remove adherent scaling
from components and to enhance aesthetic appeal of forgings.
Time required for these operations can be substantially
reduced if a coating is applied on components before heat
treatment (Endorsement 1). Aesthetic appeal of components is
automatically enhanced without much effort as scaling is either
prevented or reduced by using anti-scale coating.
3. Salvaging fully machined components by protecting
during re-heat treatment
Often, fully machined forgings need to be re-heat treated
for metallurgical reasons. However, there is no material
allowance left for further scaling to take place and for
subsequent machining or shot blasting. In such cases, even
a small amount of scaling can render components to be
scrapped. Use of anti-scale compound ensures prevention of
scaling during re-heat treatment. Hence, huge losses can be
prevented by salvaging fully machined components. Aesthetic
appeal of components is retained (Image 2). The coating itself
can be removed after heat treatment by cleaning the forging
with diesel, emery paper brushing or light wire brushing
(Endorsement 2).
Figure 2
: Benefits of using coating in processing of stainless steel
pipe fittings
Image 1
: Crank shaft gear-end section prone to quench cracking
Image 2
: Fully machined spindle re-heat treated by applying anti-
scale compound. Zero scaling observed. Aesthetic appeal is intact
PICKLING