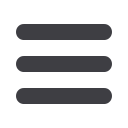

Inspection, testing & qual ity control
www.read-tpt.com92
M
arch
2015
Fluorescent crack detection
system
IN AEROSPACE applications, as well
as other sectors such as the automotive
industry, the highest quality is of decisive
importance. Even the smallest defects
can have serious consequences.
Toolcraft states that its components are
produced with the highest precision.
The quality of products can be
quickly and reliably verified by the new
system for non-destructive surface
testing. The precision parts and high-
tech components are wetted with a
fluorescent penetrant for this purpose,
making even the smallest cracks visible
under UVA light.
On an area of 105m
2
, Toolcraft can
now offer the opportunity to check
components using a non-destructive
method for cracks, overlaps, folds,
pores and binding errors in the surface.
The process is predominantly used
on metallic materials, although it can
also be applied to materials such as
ceramics, assuming the surface is
suitable for testing with penetrants. The
system itself occupies an area of 75m².
When building the crack detection
system, emphasis was placed on
cleanliness. The system and all
equipment are made from stainless
steel – a material suited to crack testing
because substances with elevated pH
values are used. Harmful, flammable
and volatile substances are employed,
as a result of which the entire area
is strictly monitored; only specialist
personnel are allowed to enter during
the test procedure.
Each testing process starts with
preliminary cleaning of the components
in an alkaline bath. Following this, the
alkali is washed off again in a three-
stage bath cascade using demineralised
water.
Once the fluorescent penetrant has
been applied by an electrostatic method,
the component undergoes intermediate
cleaning. It is then immersed in an
emulsifier bath in order to partially
dissolve the penetrant. Immersion in the
water stop bath is used for finishing the
process.
The testers apply a dry developer
before assessing the component.
This picks up the penetrant remaining
in the defects and shows it up under
UVA light. Even microscopically small
cracks are revealed in the evaluation
cabin; these are cracks that can
have a decisive effect in aerospace
applications.
In addition to a re-emulsifiable material
on quality level three (high) being used,
priority is given to regular monitoring of
the test instruments.
Before the start of each test pro-
cedure a sample plate is put through
the entire process. Existing defects are
documented according to the highest
quality standards, by qualified specialist
personnel.
Toolcraft is a partner of research and
development departments in many
industrial sectors. As an associate
of engineers and designers of
semiconductors, optical industry and
opto-electronics, special machinery
manufacturing,
motorsports
and
automotive,
medical
technology,
aerospace, defence and security, toy
and consumer goods industry, and the
printing industry, Toolcraft manufactures
precision parts, assemblies, moulds and
injection moulded parts.
MBFZ toolcraft GmbH
– Germany
Fax: +49 9172 6956 560
Email:
toolcraft@toolcraft.deWebsite:
www.toolcraft.deEven microscopically small cracks
are revealed in the evaluation cabin
Precision parts and
high-tech components
are wetted with a
fluorescent penetrant
for the testing