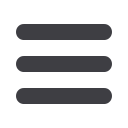

Inspection, testing & qual ity control
www.read-tpt.com94
M
arch
2015
Next-generation laser
measurement system
ETALON’S LaserTracer was developed
for the sub-micron-accurate geometric
analysis, monitoring and accuracy
improvement of machine tools and
measuring machines. It is a self-tracking
laser interferometer that automatically
tracks a reflector, and allows for the
identification of geometrical deviations
with high precision. The compensation
data determined by the system can
be directly imported into the control
software of the machine tool or CMM.
The follow-up model, LaserTracer-
NG, is an entirely redesigned system
that consolidates Etalon’s experiences
gained during the last ten years of
machine calibration. The LaserTracer-
NG is smaller, weighs less and offers
a larger angular range, to facilitate
measurement in limited machine
space. It can deal with highly dynamic
machine movements: the accelerations
of the machine permitted during
measurement have nearly doubled.
Shop floor suitability was also a
major aspect when redesigning the
measurement system. Originally, the
LaserTracer had mainly been used
under laboratory conditions. With its
more recent use in production, it faces
much harsher conditions. To prepare
the new LaserTracer-NG for these
challenging environments, it is equipped
with a closed housing, with only two
connectors, and a more flexible cable.
In
contrast
to
conventional
measurement devices, the LaserTracer-
NG features, like the previous model, an
accuracy of the centre of rotation thanks
to a patented measurement technique.
A sphere with a form deviation of just
50 nanometers is used as an optical
reference for the interferometer. As a
consequence, mechanical errors of
the rotation and swivel axes are fully
compensated.
For measurement execution, the
LaserTracer-NG is placed stationary
at several different positions inside the
working volume of the machine. The
reflector is mounted to the tool or probe.
In the following automated measuring
process, the system tracks the actual
path of the machine in its entire working
volume. Meanwhile, the system acquires
highly precise measurement values that
are processed and analysed by Etalon’s
Trac-Cal software package.
Etalon offers system solutions for
the accurate and comprehensive
geometric analysis, monitoring and
accuracy improvement of machine
tools, measuring machines and robots.
Customers include companies from
mechanical engineering, industrial
instrumentation,
automotive
and
aerospace technology, and the research
sector. Etalon is active worldwide in
the high technology markets, and
works with competent local partners to
optimally support customers. In the area
of machine compensation, Etalon is an
official Zeiss Business Partner as well
as a Siemens Solution Partner.
Etalon AG
– Germany
Fax: +49 531 70 228 99
Email:
info@etalon-ag.comWebsite:
www.etalon-ag.comTesting steel tubes
MAGNETIC Analysis Corp (MAC)
Echomac
®
ultrasonic
inspection
systems are being used by a number
of tube manufacturers who supply steel
tube for heat exchanger applications. A
recent installation at Ratnamani Metals
& Tubes Ltd, a steel tube producer in
India, is testing welded stainless steel
heat exchanger tube to meet industry
standards.
The system incorporates an Echomac
ultrasonic instrument with an ultrasonic
rotary containing eight transducers – two
for detecting longitudinal defects, two for
transverse, three for wall thickness and
OD/ID measurement, and one for water
temperature compensation to enable
dimensional measurement. This is the
second system of this type that MAC
has supplied to the company. Both are
operating very satisfactorily, according
to the company.
MAC has also supplied several
ultrasonic test systems to Schoeller
Werk in Germany, to inspect heat
exchanger tubing made of stainless
steel and titanium alloys. In addition to
detecting defects, the company uses
these systems to provide quick feedback
on changes taking place in the welding
process. One system incorporates
seven ultrasonic channels, while the
other includes 14 channels. MAC also
supplied a complete inlet table and
outlet conveyor.
Magnetic Analysis Corp
– USA
Fax: +1 914 703 3790
Email:
info@mac-ndt.comWebsite:
www.mac-ndt.comEtalon’s LaserTracer-NG