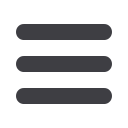

Inspection, testing & qual ity control
www.read-tpt.comM
arch
2015
95
SIDE LOADING FOR FAST TOOL
CHANGE AND NO LIFTING REQUIRED
• Infinitely adjustable
expansion & reduction
• High production
capability
• Up to Ø 152mm
• No tube clamping
required
• End form on or
near bends
• High quality build with
practical platforms
• Full 12 month warranty.
• Twin Head Machines
also available
Unit 24, Padgets Lane, South Moons Moat,
Redditch, Worcestershire B98 0RB, England.
T: +44 (0)1527 518520 E:
info@avamatic.co.ukW:
www.avamatic.co.ukGermany: Tel: 02150 2500
Netherlands/Belgium: Tel: (04756) 6888 USA: Tel: 708 272 7880
TUBE END FORMING
AV65
B-scan inspection system
SCRAP reduction is of particular
importance to the welded tube industry;
relatively small reductions in percentage
scrap can yield large savings. For
tube manufacturers, monitoring the
weld flash removal process on line
well before problems are revealed at
cut-off is an attractive scrap reduction
tool, particularly when post-weld heat
treatment imposes long cooling runs
before cut-off.
The InspecTech B-scan Inspection
System (IBIS) was first sold to the welded
tube industry more than 20 years ago.
The unit was conceived and engineered
around the ‘need to know’ the condition
of the inside flash removal process, and
the resulting scrap reduction potential.
As computing power has increased,
the performance and utility of IBIS have
improved. Displays, once delayed, have
moved to real-time, and the OD profile
of the tube has been included on the
screen in addition to the thickness scale.
InspecTech has announced new
software and firmware enhancements
that have made the IBIS
more user-friendly and
flexible. In addition, the
HMI (human-machine
interface) has been
updated and improved.
The test head of
the IBIS flash monitor
scans across the weld
zone and adjoining
parent metal covering
a band around 50mm
wide. The ultrasonic
system
makes
thousands of readings
during each sweep,
measuring both the
material
thickness
and the outer surface
profile.
Rather than a curved profile, IBIS
displays a set of Cartesian plots that
are calibrated directly in engineering
units (inches or millimetres), and which
may be used to define alarm limits
and display allowable tolerances. The
company states that this would not be
practicable in polar views.
InspecTech
– Canada
Email:
group@inspectech.caWebsite:
www.inspectech.ca