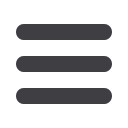

J
anuary
2016
99
Article
Schwarze-Robitec GmbH
Tube resource efficiency in
shipbuilding and plant construction
By Dipl.-Ing. (FH) Jürgen Korte, sales manager at Schwarze-Robitec
Introduction
In shipbuilding and plant construction, miles and miles of
pipelines made of the most varied materials and with variable
diameters and nominal widths are processed. That is why
high flexibility is in great demand with tube bending machines.
“Time and cost savings are achieved, for example, when
avoiding any welding of tubes,” explained Jürgen Korte, sales
manager at the bending machine manufacturer Schwarze-
Robitec GmbH.
Multi-stack CNC tube bending machines have proven
themselves in this context. They are equipped with stacked
tooling, which is capable of bending tubes with different
nominal widths on one system without any conversions.
Due to the minimised set-up times, productivity increases
massively. An advantage that international shipyards and
plant construction firms have used for themselves over recent
years.
Schwarze-Robitec from Cologne has supplied the industry
internationally with the multi-stack CNC tube cold bending
machines in the most diverse design sizes. One of these
systems is the CNC 220 HD MW of the heavy-duty series
from Schwarze-Robitec. The tube and section cold bending
machine, with 32 tons total weight, processes tubes with a
Subjects such as sustainability and green technology
have been discussed in the media for some years now, or
are used as a popular plug for corporate announcements.
Nevertheless, the reality is that the industry is still not
fully sustainable, because companies use the majority
of the gross production value for material. According to
calculations by the German Federal Office of Statistics,
that is an average 45 per cent. This results in a large
savings potential with regard to both sustainability and
company operating costs.
In view of rising costs for raw materials and energy,
one thing is sure: whoever wants to stay competitive,
must use resources sensibly, streamline production
processes and therewith increase efficiency. The human
operator should also be taken into consideration in this
context, because operator-friendly and secure production
processes make a considerable contribution to the
profitability of companies.
maximum diameter of 219.1 x 12.7mm – and that for a tube
length of up to six metres. Despite its size, the system is
unusually flexible in handling.
With the help of the stacked tooling, up to 70 per cent of
the set-up time of market-based systems can be saved. It is
possible to process tubes of different materials, such as steel,
copper-nickel-iron alloys and stainless steel on one tool.
At the same time, thin-walled and thick-walled tubes with
different diameters can be bent. With this clever tool concept,
users have the most varied material standards and tube
geometries under control.
The set-up times between the different versions are minimal:
a conversion of the system is not necessary. A further time-
saving plus of the CNC 220 HD MW is that the different
production data are stored in the control system and do not
need to be re-entered if required.
This concept has the potential to offer significant economic
advantages said Mr Korte. The quick set-up times make
sure that downtimes are short and utilisation of the machine
remains high.
“Schwarze-Robitec has already sold the machine type around
50 times to customers from the shipbuilding sector, the
chemical industry and power plant construction,” reported
Mr Korte.
Time-saving details
The production of complex three-dimensional tube systems
becomes cost-intensive, particularly because numerous
production steps are necessary. Often, each individual step
involves optimisation potential with regard to time.
Mr Korte said: “To manufacture three-dimensional tube
systems, individual bent tube pieces are welded together
and the weld seams then checked. The checking is such a
time-intensive work step, which we have abolished with our
automatic CNC machines of the HD series.”
Thereby, the tube is clamped in the index head and positioned
in space by means of the transport unit and index head.
After the first bend, it is directly transported on and turned
if necessary. This quickly creates three-dimensional tube
systems without an excess of weld seams. The tubes can
be delivered custom-fit to the building site. The use of