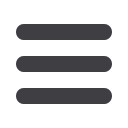

100
J
anuary
2016
Article
Schwarze-Robitec GmbH
flanged tubes in shipbuilding and plant construction also
causes additional processing steps in forming, for example
the subsequent flanging of finished tube bends. A remedy
is flanged tube facilities, which take the flange and sleeve
positions before the bending process into consideration.
In this manner tubes that are already flanged can be bent
economically.
The heavy-duty systems from Cologne’s bending specialist
are designed for the forming of double-walled tubes and
flanged tubes. These can be implemented in existing systems
ready-to-install after bending.
Another “time saver” is the marking facilities, which mark the
positions on the tubes where welds or bypasses
are to be carried out after bending. By this
procedure, the facility takes the load off the
operator, who now no longer has to conduct
time-consuming calculations for subsequent
determination of the corresponding points on
the bent tube.
Reduced material input
Tube runs in ships, as well as in offshore
and chemical facilities, offer great potential for
material savings because the long stretches of
tube cause considerable material costs.
The tube materials used in the industry sector
are also very high quality and need to be
installed efficiently. One option is small bending
radii. They optimise tube runs enormously in
the case of tight space conditions and result in
less material input.
The CNC 320 HD from Schwarze-Robitec, for
example, produces extremely small bending
radii of 1.5 x tube diameter even for large,
very thin-walled tubes with a diameter of up to
323.9mm.
Similarly, tight radii with such large
tubes are usually only achieved with
much slower and costlier warm bending
processes or welding bends. Anyone
wanting to produce with material
efficiency will also want to avoid residual
tube lengths. Machine expansions such
as the tube residual length optimisation
from Schwarze-Robitec function like
“cost brakes”. An additional savings
potential with regard to material is the
dosing of lubricants. These counteract
the high tribological loads on tool and
work pieces, which occur during cold
bending.
With most lubricating methods the
lubricants are added in large quantities
into the tube to be bent. To remove
lubricants from the finished bent tubes
after bending, the tubes normally need
to undergo an elaborate cleaning, where further chemicals
are used in the process. A considerably lower consumption
is achieved with automatic lubricating systems. With the help
of compressed air they simply moisten the bending mandrel
surface and tube inner wall. Through this optimal dosage both
the costs and the effort for the subsequent cleaning of tube
and machine are considerably reduced. The micro-lubrication
from Cologne’s bending specialist functions according to this
principle: the lines for oil and compressed air run through
the mandrel rod all the way to the mandrel. There, the oil is
distributed by the compressed air. During the bending process
it exits from the mandrel through small drilled holes. In this
way the system combines a need-based lubrication with
minimal lubricant consumption.
The CNC 320 HD from Schwarze-Robitec produces extremely
small bending radii of 1.5 x tube diameter, even for very large,
thin-walled tubes with a diameter of up to 323.9mm
Tube cold bending machine CNC 220 HD MW from Schwarze-Robitec: Tubes with different
nominal widths can be processed quickly with the stacked tooling, which can be seen quite
clearly at the front