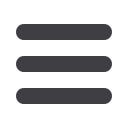

52
Wire & Cable ASIA – May/June 2017
www.read-wca.comOnly in the case of tests with a separate HV source
repeated measurements can this be done. The applied
testing voltage can be increased up to a certain voltage
level to enforce the breakdown again.
A comparison of the two TDR measurement methods is
shown in
Table 1
.
An advantage of the online method is the absence of
reflections from the far end. The breakdown causes a very
low impedance at its location and the signals are reflected
from here. A simplified circuit for online measurements is
shown in
Figure 1
.
The measurement on both cable ends with two measuring
devices improves the fault location accuracy. Of course,
this option depends on the configuration of the power
cable system and the access to its cable ends. This option
is not considered in the experimental tests yet.
Theoretical Considerations
and Simulation
The physics of cables and their behaviour is very complex
and has been widely discussed in literature. It shall not be
repeated in this paper (example for reference see
[4]
). Only
two basic equations are needed here:
When using this kind of TDR the exact knowledge of the
propagation velocity
v
determines the accuracy of the fault
location. (It differs to the TDR measurement for partial
discharge (PD) fault location where only the time relation of
the reflections determines the accuracy.)
Therefore this propagation velocity has to be known
exactly to be determined in advance. When the parameters
L’
and
C’
of the cable are effectualy known, the propagation
velocity can be calculated by
Equation 1
. However, if it
is possible, an initial measurement of the propagation
velocity should be done for each commissioned cable.
The situation changes when the TDR signals are measured
on both cable ends. Then the knowledge of the velocity is
not necessary (similar to the PD fault location) and the fault
location is calculated by:
with
T
x
and
T
y
as the signal propagation measured from
both cable ends. Of course, the calculation by knowledge
of the propagation velocity is still valid and the
measurements can be verified when the right cable length
is also known.
The test circuit was simulated with OrCAD PSpice and
with realistic cable parameters
[5]
. It allows the simulation of
the signal propagation in very long cables and the signal
distortion by the measuring circuit on the cable end.
The simulation was made with a cable length of 100km
and a propagation velocity of 171.25m/µs. The failure was
simulated at a distance of 83km from the cable end where
the measuring circuit was connected.
The simulation results in
Figure 3
show a time
T
= 970 µs
and with the aforementioned velocity
v
the distance to
the failure is calculated to
l
x
= 83.06km. The negligible
deviation from the reference value is the result of a slightly
inaccurate time measurement of the simulation results.
Measuring Equipment
The measuring circuit consists of two main components,
the HV divider and the transient recorder. While only one
type of transient recorder processes the signals from
measurements on AC and DC cables, the HV dividers differ
for AC and DC applications.
A capacitive HV divider is preferably used for
measurements on AC cables. For DC cables a
broadband divider with a resistive arm is necessary
to achieve the required response characteristic. This
response characteristic is also essential when other
voltage measuring devices are taken for the online
TDR measurements, eg instrument transformers which
are installed in power nets. Their ability has still to be
approved.
Capacity
to ground
HV
AC/DC
source
❍
❍
Figure 1
:
Principle circuit for online fault location
Equ. 1
Equ. 2
Equ. 3
❍
❍
Figure 2
:
Simulated circuit
❍
❍
Figure 3
: Simulation results