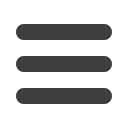

9
Chemical Technology • June 2015
WASTE MANAGEMENT
Conventional Power Station
Natural gas (grammes per gigajoule) Oil (grammes per gigajoule)
Coal (grammes per gigajoule)
0
590
940
65
140
270
Pollutant
Usual Fuel ( Coal & Coke ) milligrams/ m
3
Usual Fuel with 15% tyres milligrams/ m
3
Percentage Change
particulates
60
60
No change
oxides of nitrogen
1180
800
-32
sulphur dioxide
500
500
No change
carbon monoxide
985
948
-4
chlorine and fluorine
1.13
1.0
-12
volatile organic compounds
129
68
-47
dioxins
0.12 nanogrammes per metre cubed
0.03 nanogrammes per metre cubed
-75
Source: Blue Circle Industries plc
Table 1.3: Emissions from Blue Circle Cauldon cement kiln during tire burning trial
clay or shale, mixed with other materials to form clinker.
Temperatures in excess of 1 400 ºC are required to produce
the cement clinker. The following characteristics make ce-
ment kilns suitable for burning tyres:
• high temperature;
• long residence time;
• oxidising atmosphere;
• high thermal inertia;
• alkaline environment;
• no ash residue;
• continuous fuel requirement.
Organic constituents are destroyed due to the high tem-
peratures, long residence time and oxidising conditions in
the cement kiln, and produce carbon dioxide and water. The
majority of the inorganic constituents combine with the raw
materials in the kiln and leave the process as part of the
cement clinker. Heavy metals remain bound in the cement
and in its subsequent use. The remaining inorganic con-
stituents are expelled to the chimney where 99,9 % should
be captured through the use of electrostatic precipitators
or filters (Parker, 1987).
Tyres are used, either chipped or whole, to replace part
of the conventional fuel. They are treated in a different
way depending on the type of cement kiln. At ‘wet’ kilns,
whole tyres are dropped into the kiln about halfway along
its length, and shredded tyres are added at the fuel end of
the kiln. The tyres are subject to the very high temperatures
inside the kiln and any residues left after burning combine
with the final product. In ‘dry’ kilns the tyres are added
either to the precalciner or into the kiln at the same end
as the feed.
If cement kiln operators want to use substitute fuels they
must apply to the Agency for permission to undertake a trial.
A full assessment is made of the possible environmental
impacts of burning substitute fuels on a case-by-case ba-
sis. Following a trial, the operator must then apply to the
Agency for permission to carry out continuous burning of
a substitute fuel.
The Agency is committed to full public consultation be-
fore and after trials. In January 1998 the Agency published
a draft protocol on the use of substitute fuels in kilns for
public consultation (Environment Agency, 1998a). The
Substitute Fuels Protocol updates the Bedford Protocol
which was issued by the former Her Majesty’s Inspectorate
of Pollution in 1994.
In most cases, the trials have shown either no change in
the concentration of pollutants or a decrease when burn-
ing tyres (Table 1.3). The emissions of nitrogen oxides are
reduced by up to 40 % due to staged combustion effects in
which less thermal nitrogen oxides are generated. Because
tyres contain iron, using them as a fuel reduces the amount
of iron oxide added to the process. An additional benefit is
that no residual ash is produced from the cement process.
Tyres are already used as a fuel in cement kilns in many
countries. The British Cement Association estimates that the
UK cement industry can potentially recover up to 190 000
tonnes of used tyres, which is equivalent to 50 % of the
annual arising of used tyres in the UK .