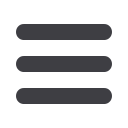

69
Focus on
www.read-eurowire.comSeptember 2012
Nov
-eurowire.comPhone:
+1. 828.885.8444
Phone USA
800.992.2402
Fax:
+1. 828 884.7494
E-mail:
Sales@KEIRmfg.comWebsite:
www.BackBoneBows.com www.KEIRmfg.comKEIRManufacturing Inc.
Features:
• Improved bow strength (no
holes)
• Wire is out of the airstream
• Bow shaped like a wing for
improved aerodynamics and
low cw factor
• Wear strip eliminated and
replaced by wear bushings
with windows for easy
inspection and dust cleaning
• Wear bushings can be
changed while bow is
mounted on the rotor
Advantages:
• Lower power (amps)
consumption and reduced
noise
• Higher TPM – maintaining
wire quality
• Reduced bow breakage
• Increased life on wear
surfaces reducing down-
times andmaintenance
• Wire breakds are contained
within the bow – extending
bow life
USPatent#
6,233,513
#
5,809,703
andOther
PatentsPending
More than a die company
Paramount Die is more than just a die company with its sales engineers
averaging over 20 years of experience in the wire industry, helping
customers with expertise in all areas of the wire drawing process.
Several trends have shaped the company’s development, including
the ever-growing need for wire drawers to outsource finished die
requirements.
As this has caused wire drawers to be become more dependent
on die suppliers, great pressure has been placed on Paramount to
increase capacity for die finishing, reduce finished die costs, and
improve lead times.
Reducing cost has been done by standardising on cost effective
carbide inserts and increasing quality and capacity through
automation. Many highly automated machines now run on “Lights
Out Operation” meaning that they will continue to produce product
as long as there is raw material being fed into the system. This not
only improves production output, but also the quality.
Average lead times have been reduced from three weeks to just
under five days. Another major wire industry trend has been the
steady increase in drawing speeds.
By placing an extreme amount of stress on drawing dies, faster
drawing speeds have further increased the importance of die design
and lubrication. In response, Paramount has worked continuously to
improve the wear resistance and strength of all its products.
Paramount Die Company – USA
Website
:
www.paradie.comCable Components Group (CCG) designs, engineers and
manufactures high performance extruded products for the
wire and cable, fibre optic and industrial markets.
CCG’s extrusion capability is predominately focused
on engineered resins, (fluoropolymers) and speciality
compounded products, (chemically foamable FEP, PFA, ETFE,
PVDF, ECTFE, etc) and uses these polymers to manufacture
tubing, tapes, crosswebs, staple fibre and non-wovens.
These products and materials characteristically provide
excellent fire retardancy, low-smoke generation enhanced
electrical performance, especially suited to the evolving
needs of the wire and cable industry. Additionally, chemical
resistance is another benefit of these engineered resins
and compounds that are targeted for industrial markets for
pipes, tubing, non-wovens for filtration, etc.
A total of 24 of the 30 CCG extrusion lines are suitable
for high temperature materials and are capable of
manufacturing foamed products, ie crosswebs, tapes, etc,
which are sold under the FluoroFoam® brand name.
The core competency of CCG, along with its 11 patents,
focuses on wire, cable and fibre optic extruded fillers and
tubes which are made for high temperature, as well as
low temperature applications. The cable fillers include
crosswebs, tapes, tubes, monofilaments and other tight
tolerance profiles for Category 6, 6e and 6A LAN cables, as
well as other industrial cables. Two new product lines are
being added to the 2012 product offering:
• FluoroSpun® – Flame-retardant non-woven tapes and core
wraps that are made from extruded fluoropolymer fibres
and made into non-wovens via needle punching or via
CCG’s revolutionary melt-blown non-woven process.
• Speciality film and shielding tape slitting – available in a
range of widths on pads or cobbs.
Fluorofoam® Masterbatch technology:
For the wire and cable market, the FluoroFoam® chemically
foamable fluoropolymer extrusion technology, which was
initially launched by CCG for category cable crosswebs and
tapes, is now being made and sold in a masterbatch pellet
form for the stringent NFPA 262 Plenum Cable Standard
(formerly UL 910).
The FluoroFoam® masterbatch pellet used for insulating
category 5e, 6, 6e, 6A and 7 LAN cable applications exhibits
extremely low levels of flame spread of 1.0ft on a 4 pair CMP
cable, as well as negligible (0.16) peak and (0.07) average
smoke generation.
FluoroFoam® is chemically foamable from a pelletised
masterbatch and can generate a range of foam rates
from 25-55 per cent. The beneficial aspects include
enhanced electricals, excellent crush resistance/physical
properties, accruing from foam cell structure of less than
0.001" on average. FluoroFoam® masterbatch chemically
foamable FEP pellets provide a unique processability,
akin to solid FEP extrusion, wherein running speeds of
1,600 to 1,800 fpm are readily attainable for thin wall CMP
communications cables.
Cable Components Group – USA
Website
:
www.cablecomponents.comHigh performance