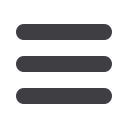

EuroWire – September 2008
32
english technology news
American Superconductor Corporation
(AMSC) has received orders for its D-VAR®
solution for grid interconnection of wind
farms located in Australia, Canada and
the United Kingdom.
The wind farms will utilise wind power
systems from three different global wind
turbine manufacturers.
The D-VAR systems, which will provide
voltage support for more than 200
megawatts (MW) of aggregated power,
will be delivered to all four wind farms
within the next 12 months. AMSC now
has an installed base and orders for
solutions to serve approximately 7,350
MW of wind power worldwide, an
increase of more than 120% over the
past year.
AMSC’s proprietary D-VAR systems
enable wind farm developers to meet
the national and provincial requirements
adopted
in
many
countries
for
connecting wind farms to power grids.
AMSC customers utilise D-VAR grid
interconnection solutions to provide
voltage regulation and power factor
correction, along with post-contingency
assistance to prevent voltage collapse on
the power grid.
“Our D-VAR solutions are being used
around the world to safely connect wind
farms to electric power grids,” said Chuck
Stankiewicz, executive vice president
and general manager of AMSC Power
Systems. “These solutions mitigate
voltage instabilities at wind farms to
enable wind farm owners and operators
to meet dramatically varying grid
interconnection requirements around
the world. This ensures the quality of the
power being delivered to customers and
in many cases improves the reliability of
the local power grid.”
Worldwide
wind
power
capacity
increased 27% in 2007 to more than 94
gigawatts (GW), according to a Global
Wind Energy Council (GWEC) report
issued in April 2008. The global wind
energy market, according to the report,
is expected to grow an additional 155%
to 240 GW of total installed capacity by
2012.
AMSC – USA
Fax
: +1 978 842 3364
Website
:
www.amsc.comFour D-VAR® orders for wind farms on three continents
Exhibited for the first time at wire 2008,
COS 1200-37 the multi-wire concentric
stranding line for screening of power
cable, from Pourtier – Gauder Group.
The machine has been designed to
produce high quality round or sectoral
compacted strands of 7, 19, 37 or 61
copper (1.5–3mm diameter) or aluminium
(2 – 3.5mm diameter) wires.
The
concentric
construction
and
multi-wire process permit speeds up
to 500rpm (compared to 200rpm with
a traditional rigid stranding line) while
keeping a short line length. Moreover,
each bobbin is equipped with an
individual driven tension control for the
prevention of wire breakage, optimisation
of the final section and, therefore,
resistance of the cable.
A 37-wire line is composed of 6
independent modules of two reels of
three wires each, individually motorised
by AC motors. Filling of the reels is made
from basket pay-offs with an individual
capstan to pull the cable and to equalise
the tension of each wire, reaching the best
winding quality.
Higher speed, smaller space, safer
production, this flexible line also allows
reduction of copper remainders, all the
parameters being adjustable from the
Colour Touch Screen Control Panel for a
better process control.
Pourtier - Gauder Group – France
Fax
: +33 1 64 26 61 10
:
sales.pourtier@gaudergroup.comWebsite
:
www.gaudergroup.comMultiwire stranding – without a break
COS 1200-37 multiwire concentric stranding line
▲
▲
Horizontal lead extruder
Since the development of the new automatic and horizontal lead extruder in 2004,
followed by the first commercial sale to Ducab in 2006, fourteen of the HFSAB
units have been sold worldwide, eight of which have already been delivered and
commissioned.
The machine's automatic and accurate operation ensures a high quality, continuous
production of cables, for weeks on end if required. The extruder is floor-standing
with all components readily available for ease of maintenance and a considerable
reduction in installation cost as a minimum of foundation work is required.
At the end of May 2008, HFSAB moved in to new, purpose-built facilities. These
facilities include in excess of 2,000m
2
assembly, warehousing and prototyping areas.
HFSAB – Sweden
Fax
: +46 141 203639
:
hfsab@hfsab.comWebsite
:
www.hfsab.com