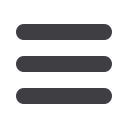

EuroWire – September 2008
36
english technology news
Er-Bakir, Elektrolitik Bakir Mamulleri AS
in Turkey, has placed an order with SMS
Meer for the modernisation of its existing
Contirod copper rod plant. The aim of the
measure is to increase the output from
currently 18t/h to 30t/h of copper wire
rod in the future. The modernisation is
scheduled for summer 2009.
Additional burners will increase the
melting capacity of the shaft furnace,
the energy efficiency will be improved
by raising the height of the existing shaft
furnace and a new higher-performance
charging system will be installed to meet
the higher melting capacity. Further
activities will include the modification of
the Hazelet twin-belt caster for a larger
casting cross-section.
At the same time, the fundamental
principle of the solidification of the melt
in a straight line with the associated
benefits for the product quality will be
retained.
SMS Meer GmbH – Germany
Fax
: +49 2161 350 1667
:
info@sms-meer.comWebsite
:
www.sms-meer.comOMCG CNC benders are available to
form wire, tube and strip or parts for
assembly, in variations to cover low,
medium or high volume up to 18,000
per hour.
CNC Feed & Form machines work with
Easy Program 3D screen animation, a
program that runs at production speed
for bend head manipulation in forming.
CNC allows forming with wire from
1mm to 18mm. The bend head allows
sharp inside radii smaller than any pin
diameter and parts can have a formed
eye on both ends. Additional ancillary
units allow coining, cold heading,
threading and welding.
With the manipulator, assembly is
possible and limited only by the
imagination of the engineer to create
the work cell. It is possible to make two
different parts on the CNC and weld
them together. With the Easy Program
on a desktop computer the program
can be prepared, tested and sent to the
CNC machine via a company network
without interfering with existing
production.
OMCG programmable slides allow quick
tool change over, some in 10 minutes.
Mechanical slides take the longest to
change over to a different part but then
run at high speed, so making up the
lost time and producing considerably
more parts at the end of the day.
To compare, CNC Feed & Form can
produce 300 parts per hour; using
OMCG programmable slides 1,500 parts
can be produced per hour while with
mechanical slides the rate increases to
3,000 to 10,000 per hour.
For long car seat wires the OMCG Turbo
is available, with two, three or four
bend forming heads and an articulate
manipulator for precise bend angle
control.
OMCG Spa – Italy
:
omcg@omcg.comWebsite
:
www.omcg.comMaximising the possibilities
of wire forming
Wire bending with CNC – limited only by the
▲
▲
imagination of the engineer
Er-Bakir modernises Contirod® copper rod plant
join us at
wire China
2008
Hall W1
•
Booth C24
SOMA is an international system and machine manu-
facturer for the fine and ultra fine wire industry.
Due to continuous improvement and expansion, the use
of modern tools and an optimal deployment of SOMA‘s
broad know how, our team is able to develop effective,
customized and competitive solutions in a very short
time (16 - 20 weeks).
Soma offers a
wide range of fine wire drawing, wind-
ing and rewinding units
. As well as pay of and take up
units. (Wire range 1,5 - 0,01 mm ≈ 0,06 - 0,0004 inch).
All our units are designed for a maximum production
output with the highest possible quality. Process stability
and optimized operating comfort are other key points of
our product philosophy.
SOMA AG
Fabrikstrasse 6
8340 Hinwil ZH
Switzerland
T +41 44 938 98 88
F +41 44 938 98 38
info@somafinewire.ch www.somafinewire.chZAM
Ultra fine wire
drawing unit
1350 x 700 x 1501 mm
ZA - Series
Intermediate, fine
and ultra fine wire
drawing unit
3182 x 1000 x 2051 mm
ZAL - Series
Break down wire drawing unit
3570 x 1000 x 2051 mm
USP
Fine and ultra
fine wire
rewinding unit
1000 x 732.5 x 1371 mm