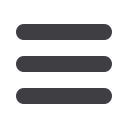

EuroWire – September 2008
37
english technology news
Where has the heat gone?
Flexible taping lines
WTM has developed new taping equip-
ment with fully motorised heads suitable
for taping and wrapping standard and
special wires and cables, even when
using the most difficult materials, due to
the high sensitivity of the electronic tape
tensioning control.
Big traverse wound spools of tape can be
used because the motor, even working at
2,500 rpm, drives the weight.
The accuracy of the taping pitch is within
hundredths of a millimetre.
The flexibility of these systems allows
production to switch from one type of
tape to another just by changing the
tape itself. Any other setting can be made
immediately by selecting the appropriate
preset values.
The taping lines are available in both
vertical and horizontal configurations to
suit the requirements of the individual
application.
Every line can be equipped with a
tele-assistance module.
WTM Srl – Italy
:
info@wtmachinery.comWebsite
:
www.wtmachinery.comBy launching the AVS, automatic winding
width control, Joachim Uhing KG GmbH
& Co offers a system to prevent the
formation of dents and bulges in the
switchover area during spool winding.
This ensures high speed unwinding
without jolts during post-processing.
“The formation of dents is particularly
critical during winding,” explains Burkhard
W Bohn, managing director for the
technology sector of Joachim Uhing.
“Dents bear the risk of slippage, followed
by bulging layers being wound on top.
During unwinding, this can cause jolts and
consequently result in material rupture.”
AVS detects even the first signs of dents
and bulges during winding. The intelligent
device memorises the respective position
and corrects the error during the next
strokes. This results in the spool being
completely filled with a continuously
cylindrical winding.
Correction occurs before the switchover
point by changing the winding width.
The stroke increases at this end when a
dent is detected. During the next strokes,
more material is fed, and the dent is filled.
In case of a bulge, the stroke decreases
accordingly, and less material is fed.
“Sensors monitor both values. The AVS
interprets an increase of the spool speed
at constant material speed as a dent since
the winding diameter must be smaller
at the deviation point, and interprets a
decreasing spool speed as a bulge.” An
additional sensor tells the controller on
which side the deviation has occurred.
The controller is suited for all winding
systems that use electrical pulses to
switch over. It can handle cylindrical
and bi-conical spools as well as conical
winding on cylindrical spool cores.
The AVS is not exclusively designed for
Uhing rolling ring drives. It can also be
implemented in other winding systems,
threaded spindle drives, or an existing
winding system can be retrofitted.
Wolfgang Weber, managing director for
Uhing Marketing asserts, “An optimum
winding result can be achieved without
manual intervention even in dirt-laden
environments.”
Joachim Uhing KG GmbH & Co –
Germany
Fax
: +49 4347 906 40
:
weber@uhing.comWebsite
:
www.uhing.comFor accurate unwinding at high speed
The new LVC/PDH rod dry preparation
and wire drawing system creates a
completely dry substitute to phosphate
and borax wet pre-coatings, enabling
high-speed direct drawing with greatly
reduced wire temperature. But where
has the heat gone?
The system permits ‘frictionless’ drawing
with a full lubricant film at the wire-die
interface in the most demanding
multi-draft applications. It provides a
strongly adherent coat for high-tensile
wire, and light water soluble coat for
plating wire.
The process uses dry coating and
lubrication technology enabling an
automatically controlled fusion of
standard dry lubrication compounds,
completely eliminating traditional wet
pre-coating chemicals and performing
as an adherent and consistent residual
coat, automatically adjustable at all
speeds.
The system eliminates wet pre-coating
chemicals and permits frictionless
drawing at 18m/s with H/C spring
wire drawn directly from mechanically
descaled bare rod. It facilitates die
wear of 0.30-0.50 micron per tonne
of wire drawn directly from 0.88%C
mechanically descaled bare rod.
The system allows an output of
2.2 tonne per hour with 5.5mm
mechanically descaled 0.83-0.88%C
bare rod drawn directly without wet
pre-coating chemicals.
Decalub – France
Fax
: +33 1 6020 2021
:
info@decalub.comWebsite
:
www.decalub.comRod/wire dry coating by LVC/PDH system,
▲
▲
in a 0.88%C application
AVS, automatic winding width control from
▲
▲
Joachim Uhing
Advertorial on behalf of Decalub