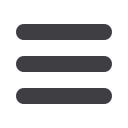

9
March 2015
AFRICAN FUSION
SAIW: Thermal spray coatings seminar
key disadvantage, however, is that the
consumable must be available as wire.
Typical uses include: aluminium or
zinc coatings for corrosion mitigation;
salvage, build-up and repair of pitting
damage, casting defects and/or wear
damage; the reclamation of steel and
cast iron parts, typically using NiCr,
NiCrAl alloys; the repair of aluminium
and magnesium alloy parts, “although
cold spray is fast becoming the preferred
process here”; and aluminium-based
coatings for anti-skid wear resistance.
The twin wire arc spray process is
commonly used for onshore wind tow-
ers, where a zinc layer is sprayed onto
the area around the flange connections
andaccessdoors for cathodicprotection.
Arc sprayed aluminium is widely used to
protect offshore steel structures, such
as offshore wind turbine foundations,
fromseawater corrosion. This is the only
coating option that is truly effective in
the highly corrosive splash zone, where
the water line meets the air.
Plasma spray coating
As the heat source, the plasma spray
coating process relies on a highly con-
trolled plasma arc, struck between a
tungsten cathode and a copper anode
within the plasma gun. An inert or reduc-
ing gasmix is fed into the space between
the anode and cathode, where it is
ionised and dissociated in the arc, trans-
forming the gas into a plasma stream of
charged particles. The plasma passes
through a nozzle as a high velocity jet
and recombines into the gas phase
along the way, releasing heat energy
that raises the gas temperature to up
to > 10 000 °C. A powder consumable is
injected into this hot gas/plasma stream,
where it is melted or softened and pro-
pelled onto the substrate.
Ideal for materials with very high
melting points, such as oxides, interme-
tallics, and refractory metals, Lovelock
says, “through a combination of high
temperature, high energy, a relatively
inert spraying medium and fairly high
particle velocities, the process produces
high quality coatings”.
The gasmixtures used strongly influ-
ence energy content and temperature. A
mixture of two gases, selected from Ar,
He, H
2
and N
2
are typically used, with N
2
and H
2
mixes offering higher enthalpy
of melting (heat of fusion) for higher
temperaturematerials and Ar and/or He
being more suitable for materials that
melt or vaporise easily.
“A wide variety of powders are avail-
able with the finer powders (5-25
m)
offering smoother and denser coatings.
There is a need to balance economics of
the process, i.e. high deposition rate vs.
the ability to melt or soften the powder
sufficiently. If the feed rate is too high,
unmelted particles and/or a low depo-
sition efficiency will result,” she warns,
adding that numerous process variables,
such as spray distance andangle, surface
speeds, heat input, cross-over speedand
the plasma arc parameters need to be
understood and optimised for success-
ful results.
Plasma spraying can also be done
in various low pressure or soft vacuum
atmospheres (LPPS/VPS), for reactive
metals such as titanium alloys – and
underwater spraying is also possible,
though seldom used.
In terms of porosity, oxides and
bond strength, plasma spray offers bet-
ter results than the conventional flame
and arc spray processes and “the coating
bond strength can be nearly as good as
HVOF coatings. For carbides, however,
bonding is not as goodasHVOF. Carbides
are not aswell retained in thematrix and
tungsten and chrome carbides begin
to decompose because of the higher
temperatures,” Lovelock adds. As well
as the high capital cost, the only other
disadvantage is that the consumables
must be in free-flowing powder form.
Uses include:
•
Aluminium and Al alloys: for build-
up and repair of Al/Mg parts (al-
though cold spray is now becoming
preferred).
•
Copper alloys: In the printing indus-
try, for example, copper and CuAl
is used and for build-up of copper
print rolls. CuNi alloys are applied
to resist fretting and cavitation and
CuNiIn alloys are used on turbine
blade roots.
•
Molybdenum: Mo-NiCrSiB coatings
offers a high bond strength, good
sliding wear and scuffing resistance
and a low friction coefficient, mak-
ing these coatings ideal for piston
rings in large diesel engines.
•
Titanium, tantalum, tungsten al-
loys, which can be used for corro-
sion resistance in chemical plants
if properly sealed. These alloys are
best deposited using VPS/LPPS,
however, andcold spray is becoming
the preferred process for depositing
Ta and Ti alloys. Ti and Ti-6Al-4V is
widely used for medical implants.
Other applications include: the ap-
plication of CoNiCrAlY coatings for re-
sistance to high-temperature oxidation.
These are used as bond undercoats for
thermal barrier coatings (TBCs) – which
are later applied using ZrO
2
stabilised
with MgO, Y
2
O
3
, CaO, CeO
2
, and others
– and the nickel-aluminium/nickel-
chrome (NiAl, NiCrAl, NiCrAlMoFe, NiCr)
alloys, for salvage and repair applica-
tions and as bond coats under oxide-
based layers.
Pure alumina (Al
2
O
3
) has high di-
electric strength, is a good electrical
insulator and is very hard and abrasion
resistant. Adding TiO
2
to Al
2
O
3
makes
the surface less electrically insulating
and decreases resistance to chemical
attack, but adds toughness and makes
finish grinding easier. Pure TiO
2
resists
static build-up, is abrasion resistant and
chemically inert inmany environments.
Its sliding wear resistancemakes it ideal
for textile guides/rollers, pump plungers
and mechanical seals in the chemical
industry.
“Plasma sprayed chromium oxide
(Cr
2
O
3
) coatings are applied to resist
corrosion, sliding wear, abrasion, and
low-angle erosion at up to about 600 °C.
Thermal conductivity is quite high com-
pared to other oxides and it is used for
pump impellers and housings and, in the
printing industry, because the coating
is laser-engravable, it is used for Anilox
rolls that areprecisely textured to control
ink transfer.”
HVOF
The HVOF process evolved from Union
Carbide’s Detonation flame spraying
(D-gun) process, which was a propri-
etary technology of Union Carbide from
the 1960s, and was the only supersonic
flame spraying system available until
the early 80s when HVOF was developed
as a commercially available alternative.
An HVOF WC-Co-Cr coating being applied to a hydraulic
cylinder.
Courtesy of Kennametal Stellite.