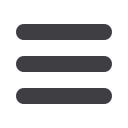

11
March 2015
AFRICAN FUSION
SAIW: Thermal spray coatings seminar
With a nozzle design based on jet engine technology, HVOF dif-
fers from conventional flame spraying in that combustion is internal
and the gas flow rates and delivery pressures are much higher. HVOF
torches generate a supersonic flame with characteristic shock dia-
monds. “Very high particle velocities are achieved, but at the relatively
low temperatures of a combustion process. This combination makes
it the ideal process for modern wear resistant carbide coatings,” says
Lovelock.
The HVOF process produces exceptionally high quality cermet
coatings (e.g., WC-Co), but it is also used to produce coatings ofmetals,
alloys and (less often) oxide ceramics. Although similar in principle,
significant details, such as powder feed position, gas flow rates and
oxygen to fuel ratios, are apparent between systems from different
manufacturers. The fuel can be propylene, propane, ethylene, acety-
lene, hydrogen, natural gas, MAPP, kerosene, and others, depending
on the system design.
Combustion parameters are the most important variable in HVOF
spraying: the ratio of oxygen to fuel; volume flows of oxygen and fuel;
and combustion pressure. Powder size and shape are also important
and eachHVOF gun is optimised for a specific powder size range. Pow-
der feed rate, standoff distance and traverse speeds also need to be
taken into consideration.
HVOF coatings, because of the high velocities and moderate
temperatures, result in less oxidation, less thermal decomposition
and high impact energy. This makes them ideal for depositing ther-
mally sensitivematerials such as carbides, without degrading particle
properties. HVOF is ideal for depositing dense, highly adherent wear
resistant coatings with very low levels of oxide, porosity and unmelted
particles. Bond strengths are among the highest available, particular
for the tungsten carbide-cobalt (WC- Co) and tungsten carbide-cobalt
chrome (WC-CoCr) coatings, whichare fast becominga replacement for
hardchrome coatings. HVOF-depositedcarbide coatings have replaced
hard chrome on the landing gear cylinders of the A380 and the Boeing
Dreamliner, which have to sustain very high stresses when landing.
On the downside, it is a process suited only to automation – HVOF
guns are often manipulated by a robot – and while some internal
diameter guns are available, internal bores are usually problematic.
It is also not well suited to onsite or in-situ work.
Cold Spray coatings
Cold spray, or gas dynamic cold spray (GDCS), is a modern coating
deposition method based on accelerating solid particles in a super-
sonic gas jet at velocities up to 1 000 m/s. The particle temperatures
remain below the melting point (typically below 800 °C) while being
projected to the substrate and, on impact, are subjected to extreme
local deformation with high transient temperatures at the interface.
There are twobroad variants of the process, lowpressure andhigh-
pressure cold spray. “In low pressure systems, the powder is injected
downstream of the nozzle throat, so the feeder itself does no have to
be pressurised. These systems areavailableas portable systems for the
surface repair of aluminiumandmagnesiumor copper components,”
says Lovelock. “High pressure cold spray systems inject the powder
upstream of nozzle throat, which requires that the powder feeder be
classified as a pressure vessel,” she adds.
While the full potential of this relatively new thermal spray process
is still being developed and explored, the process is already used for
high value repairs of aeronautical components made of aluminium
and magnesium alloys; the coating of dense oxygen-free copper for
electrical conductors, additive manufacturing, titanium coating of
medical implants and the application of zinc and zinc-magnesium
alloys onto laser engravable print rolls.
The as ground finish of an HVOF applied WC 10% Co 4% Cr coating.
Courtesy of Kennametal Stellite.
The cross section of an HVOF-applied WC-Co-Cr coating. The coating
offers resistance to sliding, abrasive and low angle erosive wear at
temperatures of up to 540 °C and chromium in the matrix gives better
corrosion resistance compared to WC-Co coatings.
Courtesy of TWI Limited.
Courtesy of TWI Limited.
The cross section of an HVOF-applied Alloy 625 coating, a barrier
coating for corrosion resistance.
Conclusions
“While there aremany thermal spray processes, it is impor-
tant to select the right coating for thewear conditions, wear
mechanism, corrosiveenvironment, operating temperature
and loading requirements of the component. Tight control
of process parameters is crucial, and standards and cus-
tomer specifications are becoming increasingly stringent
as the global thermal spray industry is required to service
ever more critical applications,” Lovelock concludes.