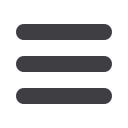

AFRICAN FUSION
March 2015
6
SAIW: Thermal spray coatings seminar
“People often don’t realise just how
important surface engineering is to
modern life. While the technology is
largely invisible, it is also indispensable,”
Lovelock begins. The general role of
surface engineering is to optimise the
surface of a component to better suit
its environment. While one can optimise
mechanical properties such as strength
and toughness of a product by selecting
an appropriate base material, surface
engineering allows one to separately
optimise the surface for better wear,
corrosion, high temperature oxidation
or thermal degradation resistance. And
the material property requirements for
the bulk materials of a product often
contradict the requirements at the sur-
face,” she points out.
Also, from a cost, design flexibility
and fabrication point of view, corrosion
and wear resistant materials are often
very difficult to fabricate or they cost
too much.
Citing some examples, she says
that in the transport industry, coating
technologies are used in catalytic con-
Introduction to thermal
spray coatings
Heidi Lovelock
On January 21, 2015, SAIW and the Thermal Spray
Association of Southern Africa (TSASA) hosted
South African-born thermal spray specialist, Heidi
Lovelock, who is now with TWI in the UK, to present
aone-day seminar at Emperor’s Palace.
African Fusion
summarises the opening session.
verter cartridges, jet engines and aircraft
landing gear. In the energy field, the
technology is indispensable for coating
solar cells, for the cathodic protection of
offshore wind turbines and, for conven-
tional fossil fuel power plants, coatings
are usedon the blades of steamturbines
and for erosion protection of critical
boiler tubes.
“In the healthcare industry, people
are living longer, so knee and hip im-
plants are needed. The success of these
depends on thermally sprayed ceramic
and titanium alloy coatings that ensure
the implant is biocompatible andable to
bind to bone,” Lovelock reveals.
Surface modification treatments
and coatings include a multitude of
processes such as carburising, nitriding
and anodising surface layers, for im-
proving the hardness of gear teeth, for
example. Hard chrome andother plating
processes, such as copper, nickel, zinc,
cadmiumand tin coatings, are inexpen-
sive but, in the case of hard chrome, in
particular, are under pressure due to
environmental considerations. Other
modern process-
es include thin
film processes
such as chemical
and physical va-
pour deposition
(CVD and PVD),
which offer layer
thicknesses from
a fewnanometres
to 50 µm; as well
as a wide range
of paints, epox-
ies, synthetic lay-
ers and powder
coatings, many of which can be very
sophisticated.
Thermal spray coating
characteristics
“Thermal spray coatings adhere via a
mechanical bond as opposed to a met-
allurgical one. Sometimes people react
to this fact with nervousness, think-
ing the surface layer can’t have much
bond strength. But it most certainly
can. Tensile bond strengths of greater
than 80 MPa are achievable but the
true strength is difficult to determine
accurately due to the limitations of the
glues used in testing,” Lovelock reveals.
“The bonding mechanisms at the
coating/substrate interface and be-
tween the coating ‘splats’ is still subject
to some speculation, though, but while
both mechanical interlocking and dif-
fusion bonding may occur, mechanical
bonding predominates.”
In principle, all thermal spray pro-
cesses involve the use of a coating con-
sumable, usually in wire or powdered
form. An energy source is used to heat
the consumable tomelt or soften it, after
which the particles are propelled toward
the surface being coated. Representing
thermal spray coating processes in two
dimensions, Lovelock displays a pro-
cess map with particle temperature on
the y-axis and particle velocity on the
x-axis. There are four broad processes:
the flame spray processes on the left
at medium temperatures and low par-
ticle velocities; the plasma processes
that give very high temperatures but
relatively low particle velocities; the
high velocity oxy-fuel (HVOF) processes,
which can produce particle velocities of
The thermal spray process map shows the combination of particle velocity
and particle temperature inherent in the different thermal spray processes.
Heidi Lovelock, surface engineering specialist with
TWI in the UK, at the TSASA-hosted thermal spray
coatings seminar at Emperor’s Palace
.
Courtesy of TWI Limited.